How to Select a Dredge Pump or Slurry Pump?
Introduction
Selecting the right dredge pump or slurry pump can be a challenging process, but understanding the primary factors behind smooth pump operation can simplify this task. The correct pump not only delivers more efficient performance but also requires less maintenance, consumes less power, and has a longer lifespan. The terms "slurry pump" and "dredge pump" are often used interchangeably.
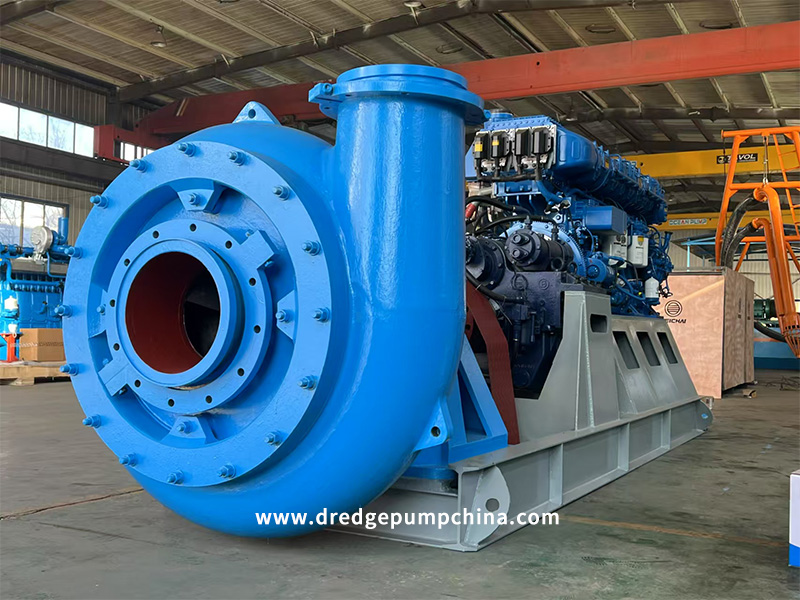
Definition of Dredge Pump and Slurry Pump
Slurry pumps are mechanical devices used for the pressure-driven transport of a fluid mixture (aka slurry). The fluid mixture typically consists of water as a liquid with solids such as minerals, sand, gravel, human waste, drilling mud, or most crushed materials.
Dredge pumps are a special category of heavy-duty slurry pumps used in the process of dredging. Dredging refers to the transport of underwater sediments (usually sand, gravel, or rocks) from one area to another. Dredging typically occurs in shallow water areas of lakes, rivers, or oceans for purposes such as land reclamation, desilting, flood prevention, creation of new ports, or expansion of existing ports. Industries that commonly use dredge pumps include construction, mining, coal, and oil & gas.
Primary Selection Requirements for Dredge Pumps
Apart from economic considerations, two primary selection criteria for dredge pump operation are:
No settlement of sediments in the pump.
Minimum wear and tear in the pump due to flow operation.
The key design parameters to keep in mind to satisfy these requirements are:
Type of installation
Critical flow rate
Total discharge head
Pump design material
Know Your Slurry Type
Before estimating the design parameters of your slurry pump, it is crucial to be familiar with the material that needs to be transported. Therefore, estimating the pH and temperature of the slurry, the specific gravity of the slurry, and the concentration of solids in the slurry is the first crucial step towards selecting the ideal pump.
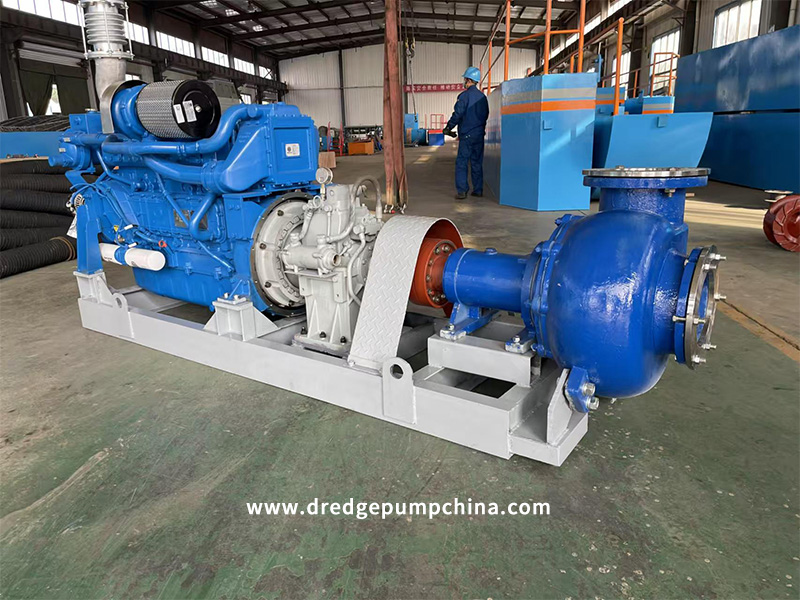
Critical Flow Rate Estimation
The critical flow rate is the transition flow rate between laminar and turbulent flow. It is calculated based on grain diameter (size of slurry particles), the concentration of solids in the slurry, and the pipe diameter. For minimal settlement of sediments, the actual pump flow rate should be higher than the calculated critical flow rate for your application. However, it is important to be careful with the selection of the pump flow rate, as an increase in flow rate will increase the wear and tear or abrasion of the pump material, thereby reducing the pump's lifetime. Therefore, for uninterrupted performance and extended lifetime, the pump flow rate should be optimized.
Discharge Head Estimation
The total discharge head is a combination of static head (actual elevation difference between the surface of the slurry source and the discharge) and friction loss in the pump. Friction loss depends on the geometry of the pump (pipe length, valves, or bends) and is also affected by pipe roughness, flow rate, and slurry concentration (or percentage of solids in the mixture). Friction losses increase with increases in pipe length, the specific gravity of the slurry, concentration of the slurry, or the slurry flow rate. The pump selection procedure requires that the discharge head of your pump is higher than the calculated total discharge head. On the other hand, it is crucial to keep the discharge head as low as possible to reduce pump abrasion due to slurry flow.
Pro Tip - Essential Questions for Pump Selection
What type of material will be pumped? (sand, mud, coarser particles, sludge, etc.)
What are the flow rate target goals? (e.g., __ m³/h)
What is the length of the pipeline? (e.g., __ meters)
What is the elevation rise of the pipeline? (e.g., __ meters)
What type of pipeline will be used? (plastic, metal, etc.)
What is the density of the material?
What is the viscosity of the material?
These items are important in determining the proper pump for your project. Hopefully, any company you get a quote from is asking these questions. This is especially important when pumping sludge, slurry, muck, mud, and other viscous materials.
Pump Power Rating
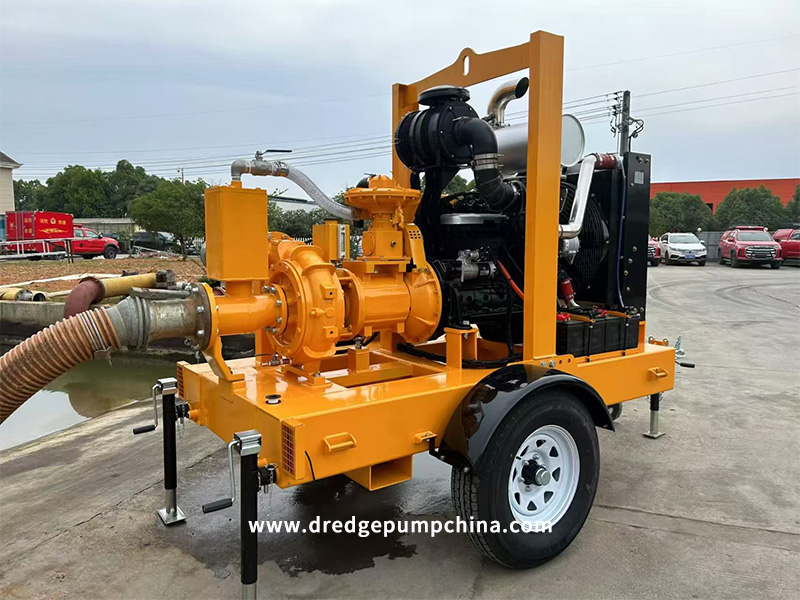
The power consumption by the dredge pump is estimated from the discharge head, flow rate, and specific gravity of the pumped slurry. It is critical to verify that the power rating of the selected pump is higher than the calculated power consumption after taking into account reasonable variations in operating conditions.
Material Selection
Typical materials used for the construction of slurry pumps are cast iron, stainless steel, and high chrome steel. Some slurry pumps come with a lining to better deal with problems of slurry abrasion. Elastomers used in the lining material include natural rubber, polyurethane, or neoprene. The selection of lining material depends on the operating temperature, pH of the slurry, and the presence of specific abrasive fluids used in the dredging process.
Type of Slurry Pump Installation
Based on the shaft orientation, slurry pumps can be divided into horizontal pumps and vertical pumps. Horizontal pumps have the shaft in a horizontal position, while vertical pumps have a vertically aligned shaft. Horizontal pumps are the most common type of slurry pump used and have the advantage of ease of installation or maintenance, a wide range of flow parameters, and choice of design materials. However, vertical pumps have the advantage of requiring relatively much less ground space for installation.
Another method to classify the type of installation for slurry pumps is dry installation or wet installation. Dry installation pumps have the hydraulic end and the drive located outside the liquid, while wet installation pumps, such as submersible pumps, operate inside the sump or the slurry. Submersible pumps do not require much support structure, hence, do not occupy much space. The preferred method of pump installation is decided based on the kind of operation and installation desired.
Specific Problems Faced in Dredge Pump Operation
Clogging:
Due to the extremely varied grain size distribution of materials handled by dredge pumps, clogging of the suction or discharge of the pumps is a damaging phenomenon that leads to expensive maintenance procedures and, more importantly, high downtime. Our patented technology at Tobee Pump has a high tolerance for the sizes of materials handled, with a capacity to handle sizes as large as 9 inches. The open rotor design allows anything that can go through the inlet to pass through the discharge without any setbacks.
Abrasion:
The massively abrasive nature of slurry¡¯s solid particles causes an enormous amount of wear and tear in pumps. Due to the harsh environments in which slurry pumps operate, Tobee Pump gives utmost importance to using the finest materials for the impeller, seal, and casing to prolong the lifetime of the pump.
Conclusion:
Hopefully, you now have a better understanding of the elements needed for proper pump selection. Even better is talking with us to help with your project-specific needs.
At TAIAN OCEAN PUMP , we are committed to providing best-in-class dredge pumps to our customers. Each component is thoroughly tested to deliver supreme quality, reliability, and versatility. Our unique technology provides us with an extraordinary capability to easily handle materials with enormous volumes and high specific gravity in tough conditions.
More inquiry £¬welcome contact
Doris Chen
WHATSAPP £º0086 18562293319
EMAIL: oc@tsbeng.com
-
WhatsApp
-
E-MailE-Mail:oc@tsbeng.com
-
WeChatWeChat:yychen19