Sand Dredging Mining Hydraulic Dredge Submersible Slurry Pump
Introduction to Sand Dredging Mining Hydraulic Dredge Submersible Slurry Pump
A sand dredging mining hydraulic dredge submersible slurry pump is a specialized piece of equipment designed for the extraction and transportation of sand and other granular materials from underwater sources such as rivers, lakes, and seabeds. It combines the functions of dredging and slurry pumping in a single unit and is typically used in the mining and construction industries.
Working Principle
Submersible Design: The pump is designed to be submerged in water or slurry. When placed in the dredging area, the impeller inside the pump starts to rotate, usually powered by an electric motor or a hydraulic motor.?
Suction Mechanism: As the impeller rotates, it creates a low-pressure area at the inlet of the pump. This low-pressure zone causes the sand-water mixture (slurry) to be drawn into the pump through the suction opening. The impeller blades then accelerate the slurry and direct it towards the outlet.?
Discharge and Transportation: The slurry is discharged from the pump at a higher pressure through a discharge pipe. The high-pressure discharge allows the slurry to be transported over a considerable distance, either to a processing plant onshore or to a barge for further transportation.
Components and Features
Impeller: The impeller is a crucial component, usually made of wear-resistant materials such as high-chromium alloys or special rubber-coated alloys. The design of the impeller can vary but is often designed to handle large-sized sand particles and to minimize clogging. Some impellers have a semi-open or open-type design to allow for the passage of larger debris.?
Motor: The motor can be either an electric motor or a hydraulic motor. Electric motors are more common for smaller-scale operations and areas with easy access to electricity. Hydraulic motors are preferred in situations where more power and torque are required, such as in deep-water dredging or when dealing with highly viscous slurries. The motor is sealed to prevent water from entering and is often equipped with cooling systems to prevent overheating.?
Casing: The pump casing is typically made of thick-walled metal or composite materials. It provides structural support to the internal components and also helps to direct the flow of the slurry. The casing is designed to withstand the pressure generated during the pumping process and the abrasion caused by the sand particles. Some casings have replaceable wear-plates to increase the lifespan of the pump.?
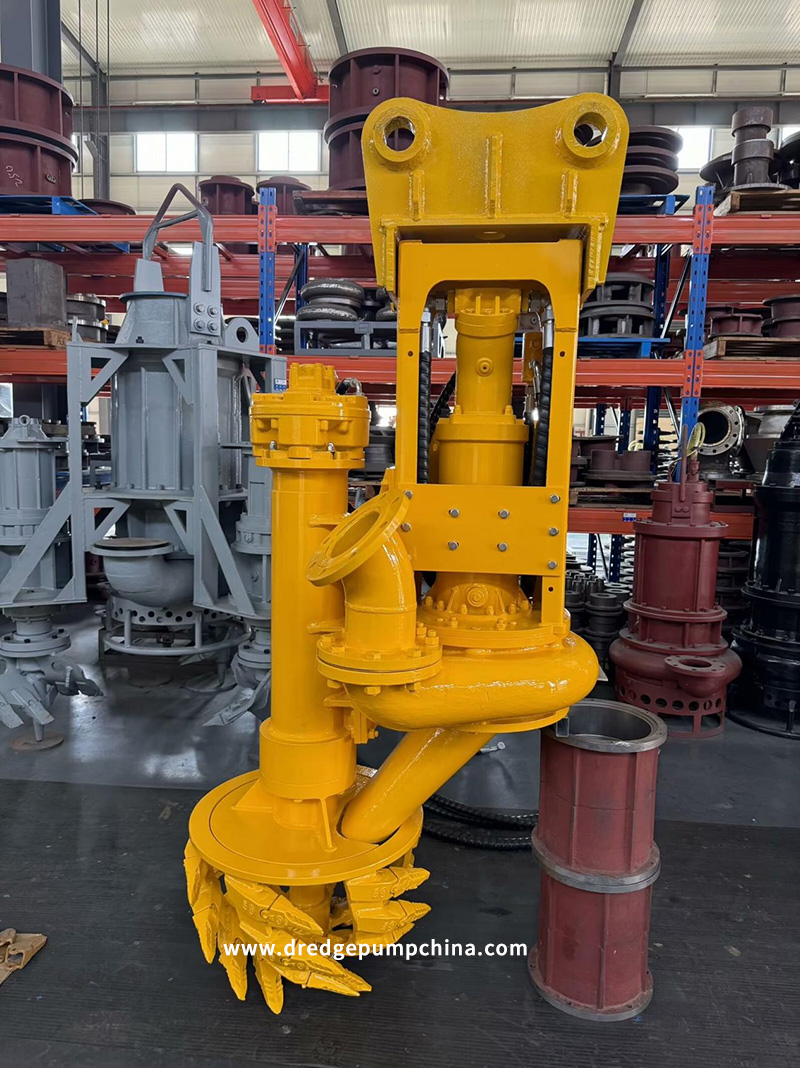
Sealing System: A reliable sealing system is essential to prevent water and slurry from entering the motor and other internal parts. Mechanical seals or lip seals are commonly used. These seals are made of materials that can withstand the harsh conditions of the dredging environment and maintain a tight seal over an extended period.?
Advantages
Efficient Sand Extraction: It can efficiently extract sand from underwater sources, increasing the productivity of sand mining operations. The submersible design allows it to work directly at the sand-bed level, reducing the need for additional equipment to bring the sand to the pump.?
Versatility: It can handle a wide range of slurry densities and particle sizes. This makes it suitable for different types of sand-dredging projects, whether it¡¯s fine-grained beach sand or coarser-grained river sand.?
Mobility and Ease of Use: Some submersible slurry pumps are relatively compact and portable, allowing for easy deployment in different dredging locations. They can be quickly installed and operated, reducing the setup time for dredging projects.?
Less Environmental Impact: Compared to some traditional dredging methods, submersible slurry pumps can cause less disruption to the surrounding environment. They can operate with a relatively small footprint and can be used to target specific areas for dredging, minimizing the impact on aquatic ecosystems.?
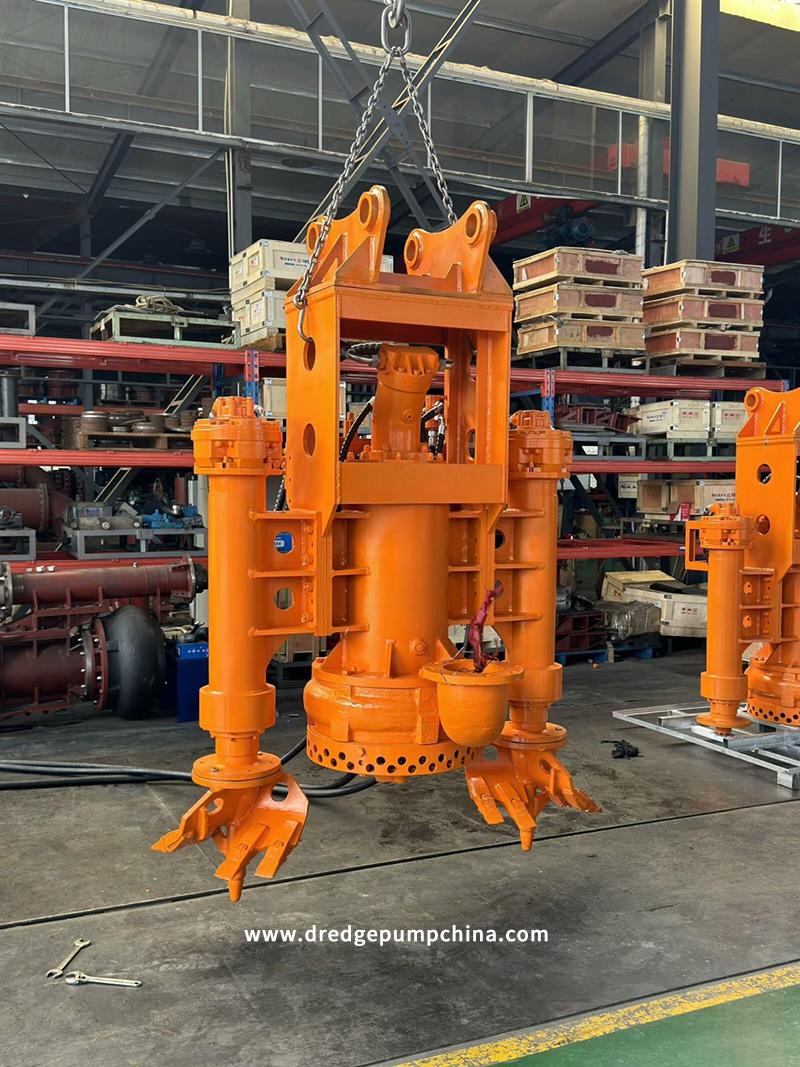
Applications
Sand and Gravel Mining: In the mining of sand and gravel from rivers, lakes, and the seabed, these pumps are used to extract the raw materials and transport them to processing plants.?
Land Reclamation and Coastal Engineering: For projects such as land reclamation, where sand is needed to fill in low-lying areas, or in coastal engineering to build breakwaters or beach nourishment, the pump can be used to dredge and transport sand.?
Underwater Construction: In underwater construction projects, such as the installation of pipelines or foundations, the pump can be used to remove sand and sediment from the work area to create a stable construction environment.?
Conclusion
Selecting the right sand dredge pump is essential for efficiency and cost-effectiveness. With over two decades of experience, Taian Ocean Pump is a trusted name in the industry, providing high-quality and reliable solutions for sand dredging and mining operations.
Hydraulic Motor vs. Electric Motor in Dredge Pumps
When comparing hydraulic motors to electric motors in dredge pumps, several key differences and considerations come into play. Here¡¯s a detailed comparison:
1.Power and Torque
Hydraulic Motors:
High Torque Capability: Hydraulic motors are known for their ability to generate high torque, making them suitable for heavy-duty applications such as deep-water dredging and handling highly viscous slurries. They can produce a significant amount of force, which is essential for moving large volumes of sand and sediment.?
Power-to-Size Ratio: Hydraulic motors have a high power-to-size ratio, meaning they can deliver a lot of power in a compact form factor. This is particularly useful in applications where space is limited.?
Electric Motors:
Consistent Power Output: Electric motors provide consistent power and are suitable for applications that require continuous operation. They are often used in more stationary or fixed applications where a stable source of electricity is readily available.?
High Efficiency: Electric motors generally have higher efficiency compared to hydraulic motors. They convert a higher percentage of electrical energy into mechanical energy, resulting in less energy waste.
?2.Efficiency
Hydraulic Motors:
Lower Efficiency: Hydraulic motors typically have a slightly lower efficiency compared to electric motors due to energy losses from fluid leaks and friction. However, they are still highly effective in heavy-duty applications.?
Efficiency Calculation: The efficiency of a hydraulic motor can be calculated using the formula:
Ehm=TTAT¡Á100Ehm?=ATTT?¡Á100
where?EhmEhm??is the hydraulic motor efficiency (%),?TTTT?is the theoretical torque (N-m), and?ATAT?is the actual torque (N-m).?
Electric Motors:
Higher Efficiency: Electric motors are more efficient, with typical efficiencies ranging between 80% and 90%. High-efficiency motors can reach up to 10% more efficiency.?
Energy Savings: Electric motors are generally more cost-effective in the long run due to their higher efficiency and lower maintenance requirements.?
3.Speed Control
Hydraulic Motors:
Excellent Speed Control: Hydraulic motors offer excellent speed control capabilities. By adjusting the fluid flow rate and pressure, the speed of the motor can be easily regulated. This makes them suitable for applications requiring precise speed control.?
Electric Motors:
Speed Control with Additional Devices: Electric motors also offer speed control capabilities but typically require additional devices such as variable frequency drives (VFDs) for precise speed control.?
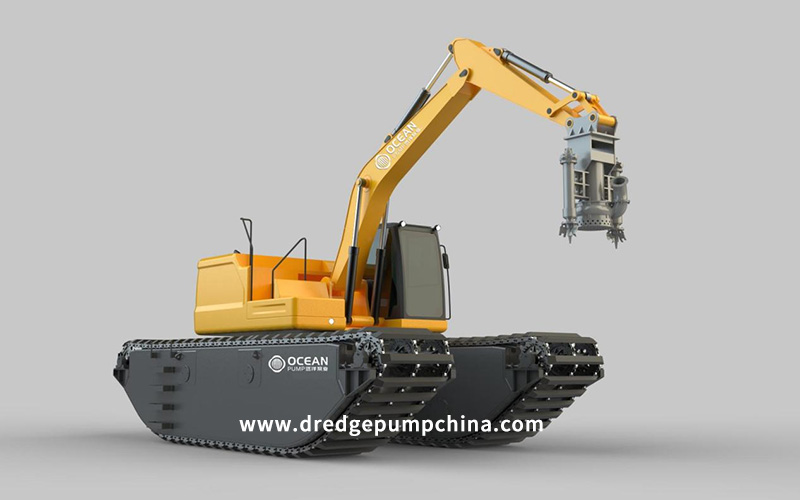
4.Maintenance and Cost
Hydraulic Motors:
Higher Maintenance: Hydraulic motors require regular maintenance, including fluid checks and filter replacements. They can be more expensive to maintain due to the need for hydraulic fluid and system components.?
Initial Cost: Hydraulic motors are usually the pricier option and can be messy to operate, with various filters, pumps, and oil requiring checks, changes, cleaning, and replacements.?
Electric Motors:
Lower Maintenance: Electric motors generally require less maintenance compared to hydraulic motors. They do not require fluid changes or filter replacements, but they may require periodic inspections and lubrication.?
Initial Cost: Electric motors are usually more cost-effective initially and in the long run due to their lower maintenance requirements.?
5.Portability and Mobility
Hydraulic Motors:
High Mobility: Hydraulic dredge pumps are highly mobile and can be easily attached to various types of hydraulic equipment, allowing them to be used in different locations and settings.?
Electric Motors:
Limited Mobility: Electric pumps may have limited mobility due to their reliance on a fixed power source, making them less flexible for remote or challenging locations.?
6.Application
Hydraulic Motors:
Heavy-Duty Applications: Commonly used in situations where heavy machinery, like an excavator, is already on-site and can provide hydraulic power. They are suitable for dredging in construction and excavation projects.?
Electric Motors:
Stationary Applications: Typically used in more stationary or fixed applications where a stable source of electricity is readily available. They are often used in industries like agriculture, mining, or sewage treatment.?
Conclusion
The choice between hydraulic and electric motors for dredge pumps depends on the specific requirements of the dredging project, the available equipment, and the location¡¯s power infrastructure. Hydraulic motors offer more mobility and are often preferred for heavy-duty, on-the-go dredging, while electric motor pumps are suitable for stationary applications with a stable power source.
If you have any further questions or need more detailed information, feel free to contact us.
TAIAN OCEAN PUMP CO.,LTD
EMAIL :oc@tseng.com
Whatsapp :0086 18562293319
-
WhatsApp
-
E-MailE-Mail:oc@tsbeng.com
-
WeChatWeChat:yychen19