Key factors in the design of centrifugal sand pump Impeller to improve efficiency
The impeller is one of the most critical components in a dredging sand pump. Its flow channel design directly affects the performance, efficiency and operational stability of the sand pump. The flow channel design of the impeller mainly includes the flow channel shape, number of blades, blade thickness, curvature, etc.
You can understand the impeller from the following aspects:
Dredge Pump Impeller basic knowledge
Material selection: The material of the impeller is critical to the performance and service life of the sand pump. Common impeller materials include cast iron, stainless steel, copper alloy, etc. Choosing the right material ensures that the impeller has good corrosion and wear resistance.and for dredging sand pump need good performance for pumping sharp sand or coal mining slurry £¬Taian Ocean Pump Co.,ltd Suggest with High Chrome alloy Cr26-28% ,With Rockness for 60 degree£¬can meet long time using .
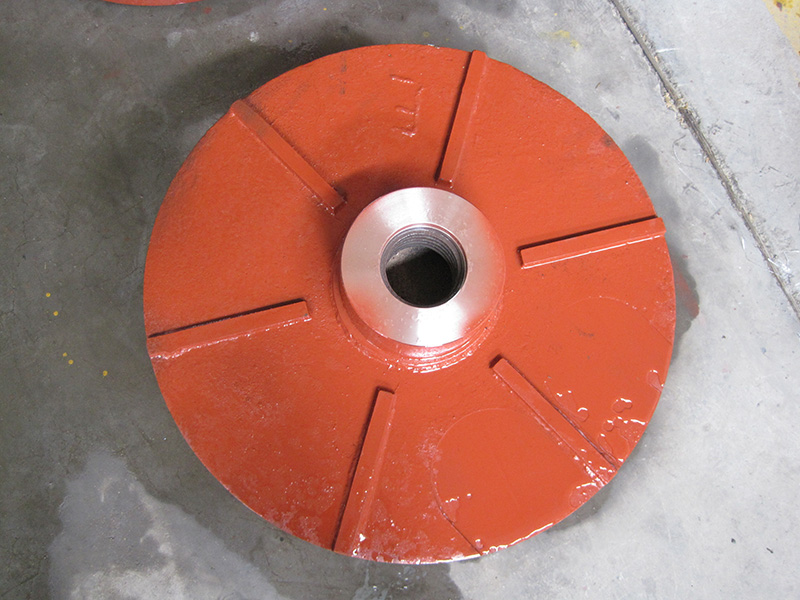
Blade design: The blade design of the impeller directly affects the efficiency and performance of the water pump. Reasonable blade design can improve the efficiency of the water pump, reduce energy consumption, and reduce noise and vibration.normally the blade number is 3 to 5 .
Blade Angle: The inlet and outlet blade angles influence the flow patterns and energy transfer within the pump. Careful optimization of these angles can minimize hydraulic losses.
Blade Curvature: As mentioned earlier, the curvature of the blades (forward vs. backward) impacts the pump's performance characteristics. This should be tailored to the specific duty point.
Blade Thickness: Thinner blades generally improve efficiency by reducing friction losses, but there is a structural integrity tradeoff to consider.
Blade Inlet and Outlet Profiles: The leading and trailing edge shapes of the blades can be designed to manage flow separation and minimize turbulence.
Blade Surface Finish: Maintaining a smooth, polished blade surface helps minimize boundary layer effects and further improve hydraulic efficiency.
Flow channel design: The flow channel design of the impeller also has an important impact on the performance of the water pump. The design of the flow channel should minimize resistance and increase the flow rate and flow rate of water.
Impeller manufacturing process: The impeller manufacturing process is also a key factor affecting the quality of the impeller. The use of advanced processing technology and technology can ensure the accuracy and stability of the impeller.
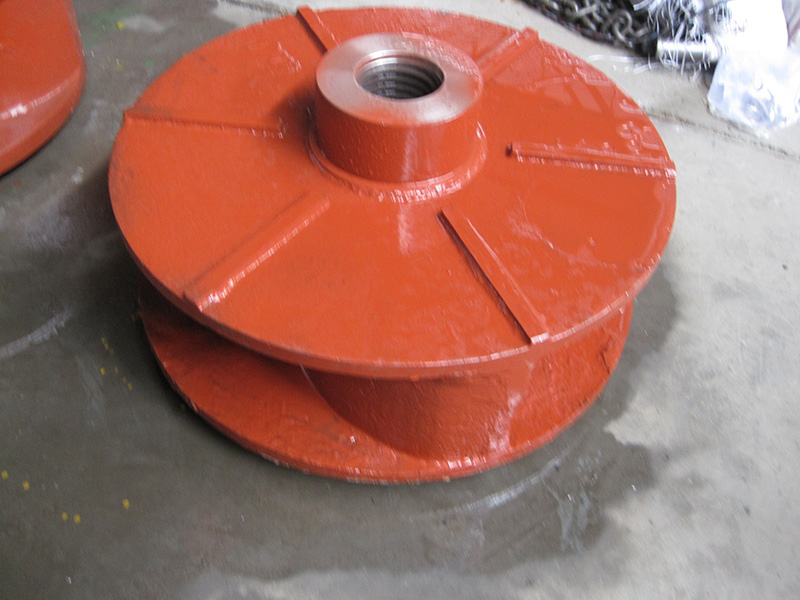
Simulation: Through technologies such as computational fluid dynamics simulation, the design of the impeller can be optimized to improve the performance and efficiency of the water pump.
Sand Slurry Pump Impeller shape
The shape of the blades has an important impact on the performance of the sand pump. Blades of different shapes will cause changes in the liquid flow direction and flow rate, thereby affecting the efficiency and wear life of the sand pump. Common leaf shapes include:
Radial flow blades: These blades are paddle wheel-shaped and convert axial flow into radial flow (i.e. from the center outward). This type of blade is simple to manufacture and is commonly used in centrifugal pumps, but is less efficient in slurry applications.
Axial flow blades: Similar to propeller or turbine blades, these blades do not change the direction of flow. They are efficient in certain applications but are prone to rapid wear in slurry pumps.
Mixed flow vane: This type of vane has a twisted design and is a type of pump between radial flow and axial flow. The specific speed of the mixed flow pump is between the radial flow pump and the axial flow pump. It is more efficient than the radial blade and stronger than the axial blade. It shows excellent performance in some applications.
Dredging Pump Impeller Blade
Impeller blade design parameters, including inlet angle, outlet angle and blade overlap, have a significant impact on pump performance.
Inlet angle: The design of the inlet angle aims to ensure that the fluid can smoothly enter the impeller at the pump's optimal efficiency point to reduce impact and turbulence, improve pump efficiency, reduce wear and prevent the risk of cavitation.
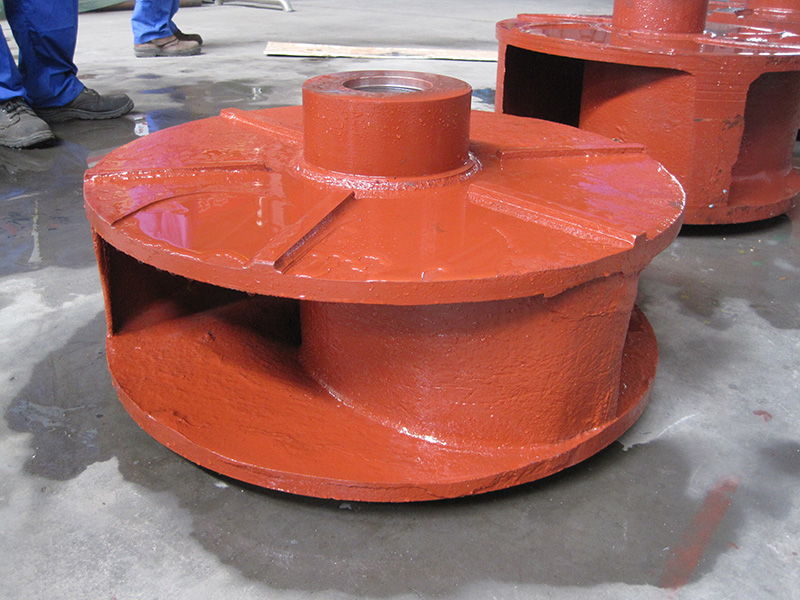
Exit angle: At a given speed, the size of the exit angle will directly affect the lift. Generally speaking, a larger exit angle can increase the head, but at the same time it will lead to a reduction in efficiency and wear performance. A smaller exit angle can improve efficiency and increase blade length, but will reduce lift, requiring a balance between lift, efficiency and wear performance.
Vane Overlap: The degree of vane overlap can affect the wear performance of the pump. Positive overlap minimizes recirculation (backflow) and helps reduce wear. For some scenarios that require lower performance, such as centrifugal pumps, performance adjustment can be achieved by cutting the outer diameter of the impeller blades. However, excessive cutting will reduce the overlap and length of the blades, so it is usually recommended to limit the overlap of the blades to about 10% of the blade diameter.
Other Factors
Flow channel shape: The shape of the impeller flow channel determines the flow pattern of water flow and pressure to a certain extent. Common impeller flow channel shapes include kinetic energy type, momentum type and combined type. The kinetic energy flow channel is suitable for high-lift pumps, and its flow channel design aims to convert the kinetic energy of the liquid into pressure energy; the momentum type flow channel is suitable for low-lift and high-flow pumps, and its flow channel design aims to convert the liquid momentum through inertia. Convert into pressure energy; the combined flow channel combines the characteristics of kinetic energy type and momentum type, and is suitable for pumps that require both lift and flow.
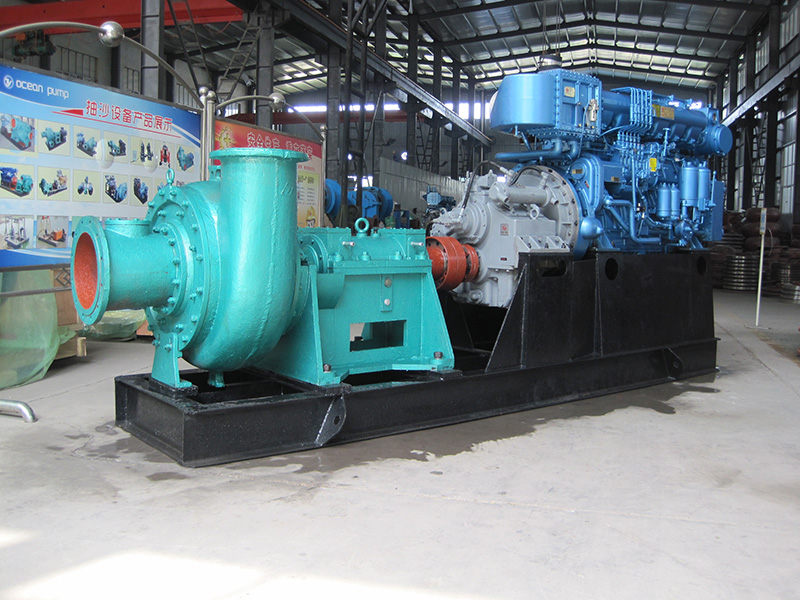
Number of blades: The number of blades in the impeller directly affects the blade gap and blade outlet area of the impeller, which in turn affects the flow, lift and efficiency of the water pump. A larger number of blades usually improves efficiency, but also increases flow channel friction loss; a smaller number of blades can reduce the blade gap and increase the open area, which is beneficial to improving flow performance.
Blade thickness and curvature: The thickness and curvature of the blades have an important impact on the aerodynamic performance and wear resistance of the impeller. Larger blade thickness will increase the resistance and pressure loss of the pump, as well as increase noise and vibration; appropriate
-
WhatsApp
-
E-MailE-Mail:oc@tsbeng.com
-
WeChatWeChat:yychen19