Wear Resistant Gravel Pump for Sand Dredging
Gravel pumps, also known as slurry or solids-handling pumps, are specifically designed to handle abrasive materials like sand and gravel.They often feature a more robust construction and specialized hydraulic design compared to standard centrifugal pumps.
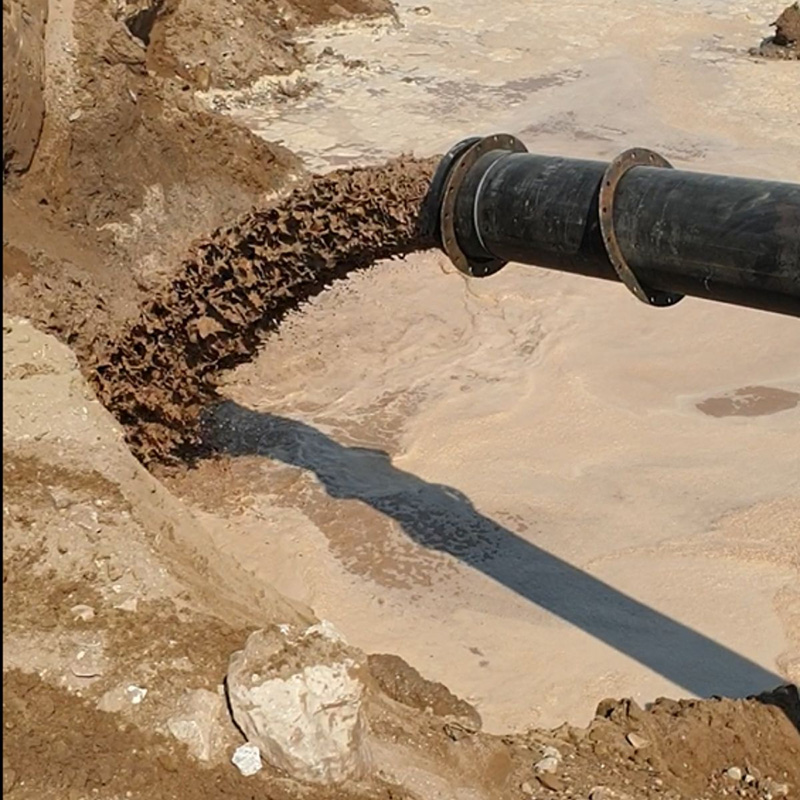
Solids Handling Capability of Gravel Pump
Gravel pumps are engineered to efficiently handle high concentrations of solids in the pumped medium.They can typically move slurries with up to 50-60% solids by volume, which is well-suited for sand dredging operations.The closed impeller and volute design helps minimize damage to the abrasive particles.
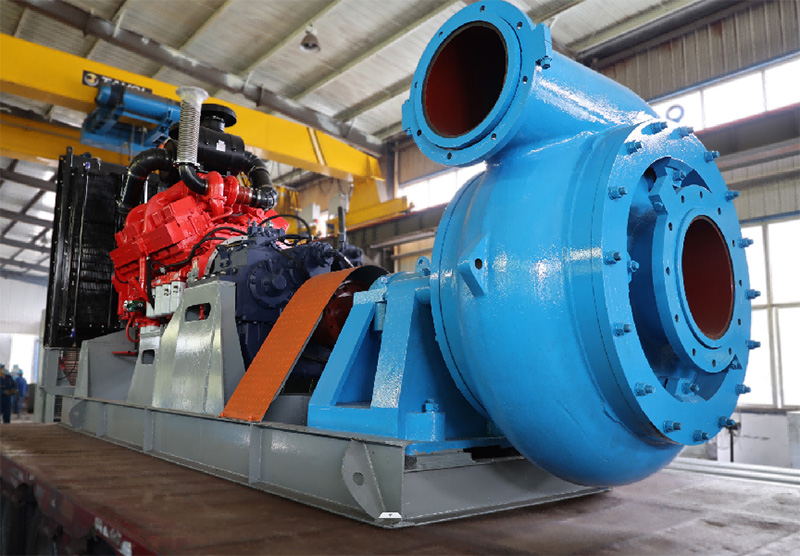
Wear-Resistant Materials of Sand Gravel Pump
The wetted components of a gravel pump, such as the impeller, casing, and liners, are made of highly wear-resistant materials Including the rock hardness for 60 degree .
Common options include rubber-lined steel, chrome-alloy steel, or high-chrome cast iron.
These materials help prolong the pump's service life in the abrasive sand dredging environment.
When selecting the appropriate wear-resistant material for the wetted components of a gravel pump, there are several key factors to consider:
Abrasiveness of the Pumped Media:
The hardness, size, and concentration of the abrasive particles (sand, gravel, etc.) in the pumped slurry are crucial factors.
More abrasive media requires materials with higher hardness and better abrasion resistance.
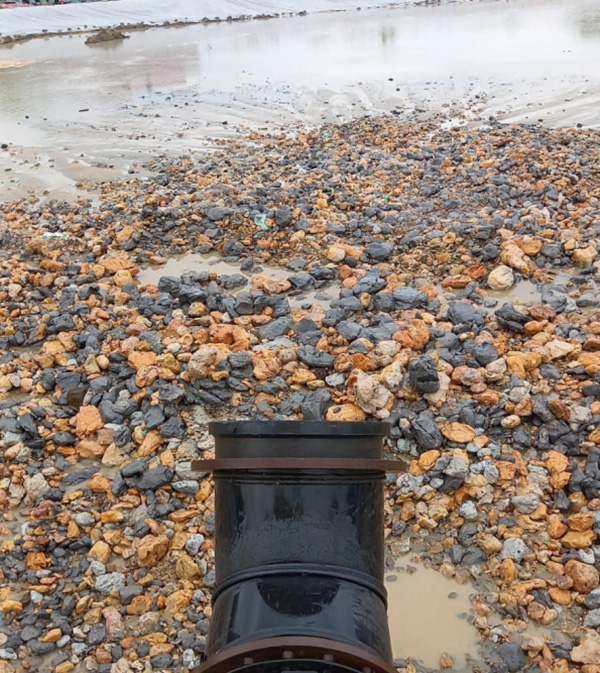
Operating Conditions:
The pump's operating pressure, temperature, and flow rate can affect the wear rate of the materials.
Higher pressures, temperatures, and flow velocities generally increase the wear on the pump components.
Corrosion Resistance:
The pumped media may contain corrosive elements, such as salts or acids, which can cause additional degradation of the materials.
Selecting materials with good corrosion resistance is important to prevent premature failure.
Mechanical Properties:
Factors like tensile strength, impact resistance, and fatigue life must be considered to ensure the materials can withstand the dynamic stresses in the pump.
A balance between hardness and toughness is often desired.
Maintenance and Serviceability:
The ease of maintenance, inspection, and replacement of wear components should be taken into account.
Some materials, like rubber linings, may require more frequent replacement compared to hard alloys.
Cost and Availability:
The cost of the wear-resistant materials and their availability can impact the overall pump design and operational expenses.
A cost-benefit analysis is often necessary to find the optimal balance between performance and economic considerations.
Industry Standards and Regulations:
Certain industries or applications may have specific standards or regulations governing the materials used in gravel pumps.
Compliance with these requirements must be ensured during the material selection process.
By carefully evaluating these key factors, pump manufacturers and operators can select the most appropriate wear-resistant materials for the wetted components of a gravel pump, ensuring reliable and efficient operation in the abrasive sand and gravel dredging environment.
Sand Gravel Pump Sizing
When selecting a gravel pump for sand dredging, consider the required flow rate, total dynamic head, and solids handling capacity.Pumps are typically sized based on the specific project requirements, such as the dredging depth, pipeline length, and solids concentration.
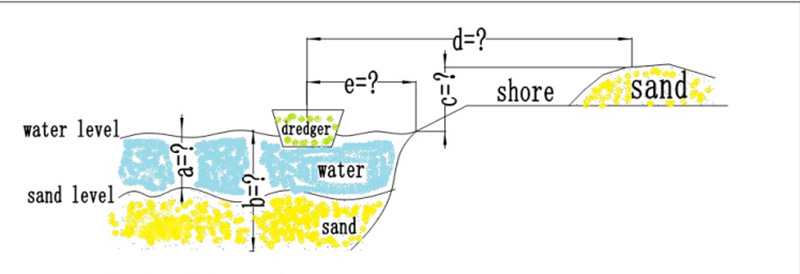
Oversizing the pump can lead to inefficient operation and increased energy consumption.
According to this drawing ,pls let us know the Answers
A. Water Depth:
The water depth is an important parameter that determines the submergence of the gravel pump and its ability to effectively draw in the slurry.
The water depth must be sufficient to ensure the pump intake is submerged and can efficiently suction the abrasive sand and gravel from the bottom.
B. Dredge Depth:
The dredge depth refers to the maximum depth at which the gravel pump can effectively operate and extract the material from the bottom.
This depth is influenced by factors like the pump's suction capabilities, the length of the suction pipe, and the desired excavation depth.
C. Vertical Height From Water Level to Stockpile:
This parameter represents the elevation difference between the water level and the desired discharge or stockpile location.
The gravel pump must be able to generate sufficient discharge head to overcome this vertical lift and deliver the slurry to the intended destination.
D. Discharge Distance:
The discharge distance refers to the horizontal distance over which the gravel pump needs to transport the slurry from the water's edge to the stockpile or disposal area.
This distance affects the overall piping requirements and the pump's discharge capabilities.
E. Discharge Distance in Water:
This parameter specifically refers to the portion of the discharge distance that is within the water body.
It is important to consider the submerged discharge distance, as it can impact the pump's performance and the handling of the slurry.
F. Sand Size:
The size of the sand particles in the pumped slurry is a crucial factor that determines the selection of the wear-resistant materials for the gravel pump.
Larger and more abrasive sand particles require more durable materials, such as tungsten carbide or high-chrome alloy steel, for the wetted components.
G. Sand Capacity Per Hour:
The sand capacity per hour refers to the volume or mass of sand that the gravel pump can handle and transport within a specific time frame.
This parameter is essential for sizing the pump and ensuring it can meet the desired production or dredging requirements.
Suction and Discharge Considerations
Ensure the sand dredge pump suction and discharge connections are compatible with the dredge pipeline and other system components.Smooth transitions, gradual bends, and a properly submerged suction inlet can help optimize the pump's performance.Incorporate features like wear-resistant liners or replaceable wear plates at the suction and discharge ports.
here's some guidance on determining the optimal discharge distance and vertical height requirements for a gravel pumping system:
Discharge Distance:
The discharge distance is primarily determined by the location of the desired discharge or stockpile area relative to the water body.
Factors to consider:
Horizontal distance from the water's edge to the discharge point
Accessibility and terrain along the discharge route
Available space for the discharge piping and equipment
Rule of thumb: Minimize the discharge distance as much as possible to reduce piping requirements, pressure losses, and energy consumption.
Vertical Height:
The vertical height, or lift, refers to the elevation difference between the water level and the discharge or stockpile location.
Factors to consider:
Depth of the water body
Desired height of the stockpile or discharge area
Elevation changes along the discharge route
Calculating the vertical height:
Measure the water depth at the pump's location
Determine the desired discharge or stockpile height above the water level
Add the water depth and the discharge height to obtain the total vertical lift
Optimizing the Discharge Distance and Vertical Height:
Analyze the site conditions and layout to find the most efficient and cost-effective configuration.
Minimize the overall discharge distance and vertical lift to reduce the system's power requirements and operating costs.
Consider the use of intermediate booster pumps or multiple discharge points to manage long discharge distances or high vertical lifts.
Evaluate the trade-offs between discharge distance, vertical height, and the overall system performance and cost.
Estimating the Required Pump Capacity:
Based on the determined discharge distance and vertical height, select a gravel pump with the appropriate flow rate and discharge head capabilities.
Consult pump manufacturers or industry guidelines to size the pump accurately.
Factor in additional pressure losses due to pipe friction, valves, and other system components.
By carefully considering the discharge distance and vertical height requirements, along with other key factors such as the abrasiveness of the pumped media and the desired production rate, you can optimize the design and selection of the gravel pumping system for reliable and efficient operation in high-abrasion applications.
How can I estimate the power requirements and energy consumption of the gravel pumping system based on the discharge parameters?
To estimate the power requirements and energy consumption of a gravel pumping system based on the discharge parameters, you can follow these steps:
Determine the Total Dynamic Head (TDH):
The TDH is the sum of the static head (vertical lift) and the dynamic head (friction losses in the piping and fittings).
Static head (H_s) = Vertical height from water level to discharge point
Dynamic head (H_d) = Friction losses in the discharge piping, fittings, and valves
TDH = H_s + H_d
Calculate the Friction Losses:
Use the Darcy-Weisbach equation to estimate the friction losses in the discharge piping:
H_d = f ¡Á (L/D) ¡Á (V^2/2g) Where:
f = Friction factor (dimensionless)
L = Length of the discharge piping (m)
D = Diameter of the discharge piping (m)
V = Velocity of the fluid in the piping (m/s)
g = Acceleration due to gravity (9.81 m/s²)
Account for additional losses in fittings, valves, and other components using appropriate loss coefficients.
Determine the Required Pump Power:
Use the following formula to calculate the required pump power (P):
P = (Q ¡Á TDH ¡Á ¦Ñ ¡Á g) / (¦Ç_p ¡Á 1000) Where:
P = Pump power (kW)
Q = Pump flow rate (m³/s)
TDH = Total dynamic head (m)
¦Ñ = Density of the pumped fluid (kg/m³)
g = Acceleration due to gravity (9.81 m/s²)
¦Ç_p = Pump efficiency (dimensionless)
Estimate the Energy Consumption:
To calculate the energy consumption (E) of the gravel pumping system, multiply the required pump power (P) by the operating time (t):
E = P ¡Á t Where:
E = Energy consumption (kWh)
P = Pump power (kW)
t = Operating time (hours)
Remember to consider the following factors when estimating the power requirements and energy consumption:
Actual pipe routing and fittings used in the system
Specific gravity and viscosity of the pumped fluid (sand-water slurry)
Pump efficiency (usually provided by the manufacturer)
Operating schedule and duty cycle of the gravel pumping system
Maintenance and Monitoring
Regular inspection and maintenance of the gravel pump are crucial to prevent breakdowns and ensure reliable operation.Monitor wear on the impeller, casing, and other wetted components, and schedule proactive replacements as needed.Maintain proper lubrication of the bearings and seals to extend the pump's service life.
Selecting the right gravel pump for sand dredging requires careful consideration of the project-specific requirements, site conditions, and operational demands. Consulting with experienced dredging equipment suppliers can help ensure the pump selection and installation are optimized for the application.
Written by
TAIAN OCEAN PUMP CO.,LTD
DORIS CHEN
WhatsApp : +86 18562293319
Email :oceanpump12@tsbeng.com
-
WhatsApp
-
E-MailE-Mail:oc@tsbeng.com
-
WeChatWeChat:yychen19