How to Extend the Sand Discharge Distance with Sand Booster Pumps?
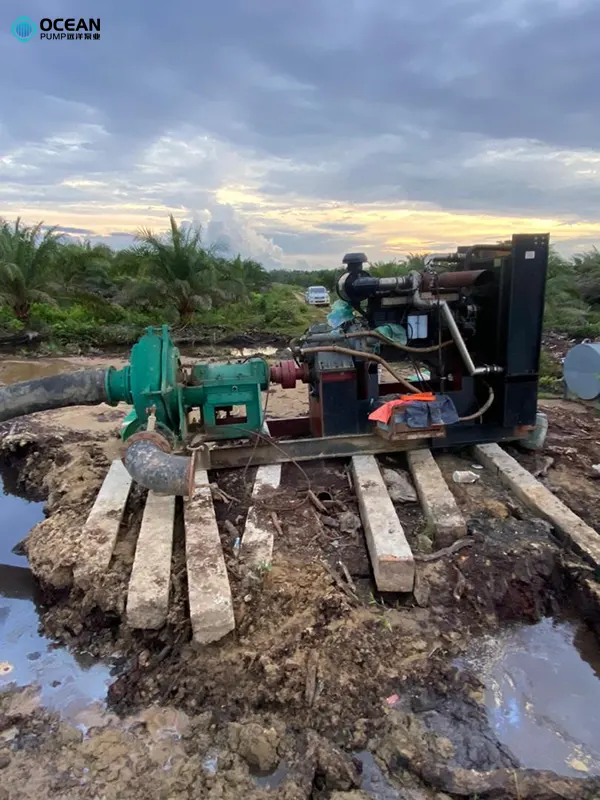
In dredging or sand mining projects, different discharge distances may occur. For example, the discharge distance at Site A is 500m, and at Site B it is 1000m. When the head of a single pump is insufficient to transport sediment to the target distance, booster pumps can be used to extend the discharge distance. The following are the specific methods:
Applicable Scenarios
- The discharge distance exceeds the maximum conveying capacity of a single pump (e.g., > 3km).
- The terrain is complex (such as having slopes and many elbows, resulting in large pressure losses).
- High - concentration slurry (with a solid content > 30%, causing high frictional resistance).
1.Working Principle of Sand Booster Pumps
The function of a booster pump (pressure increasing pump) is to increase the pressure in the middle of the pipeline, compensating for the hydraulic losses (frictional resistance elevation difference) caused by long distance transportation to ensure that the slurry can reach the end point smoothly.
2. Arrangement Methods of Booster Pumps
(1) Series Boosting
Install a booster pump at certain intervals (such as 3 - 5km) on the main pipeline to increase the pressure step by step.
Example (Taking a 16 - km Discharge Distance as an Example)
Pump Name | Function | Head | Installation Location |
Dredge Pump | Suck sand and initially pressurize | 40m | On the dredger |
Booster 1 | Boost pressure at 3km | 35m | Maintain pipeline pressure |
Booster 2 | Boost pressure at 8km | 35m | Prevent pressure drop |
Booster 3 | Boost pressure at 13km | 30m | Finally transport to the storage yard |
Key Points
- The inlet pressure of each booster pump should not be too low (to avoid cavitation).
- The head of the booster pump needs to match the pipeline frictional loss (which needs to be calculated).
(2) Parallel Boosting
If the flow rate of a single pump is insufficient, multiple pumps can be connected in parallel to increase the total flow rate (suitable for large flow and short distance projects).
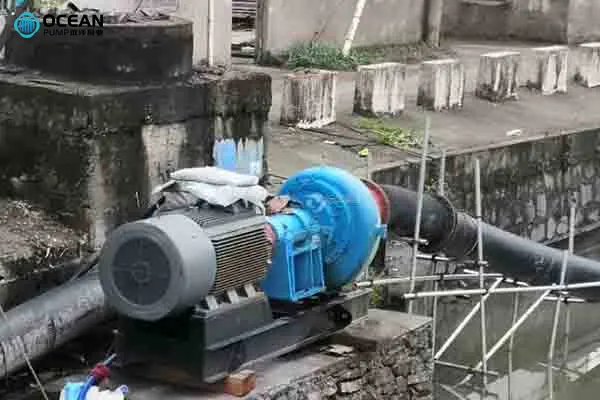
3. Key Parameters for Selecting Booster Pumps
When selecting a booster pump, the following data need to be calculated:
1. Total Pipeline Friction Loss
- Calculate using the Darcy Weisbach formula or the Hazen Williams formula.
- Influencing factors include pipeline material (HDPE/steel), diameter, slurry concentration, and flow velocity.
2. Required Head
- Total head = Elevation difference + Friction loss+ Residual pressure (safety margin).
- For example, for a 16 - km discharge distance 20m elevation, 3 - 4 booster pumps may be required.
3. Pump Compatibility
- The flow rate (m3/h) of the booster pump must be the same as that of the main pump to avoid blockage or overpressure caused by flow rate mismatch.
- The motor power needs to be adjusted according to the slurry density (higher concentration slurries require greater power).
4.Precautions for Installing Booster Pumps
Location Selection
- Install on a flat and stable ground as much as possible (to avoid vibration).
- Be close to the main pipeline to reduce elbows (to reduce local resistance)
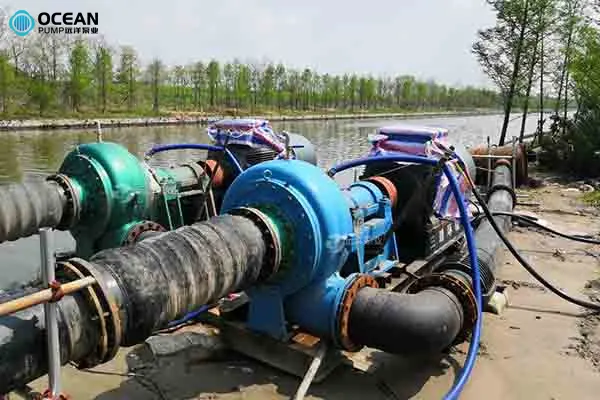
Control System
- Adopt PLC automated control to monitor pressure and flow in real - time and automatically start and stop the booster pumps.
- Install pressure sensors to prevent overloading or idling.
Maintenance Key Points
- Regularly check the wear of seals, bearings, and impellers (mud pumps are prone to wear).
- Keep one spare pump to prevent work stoppage caused by sudden failures.
5. Practical Case References
With the deep - rooted concepts of environmental protection and green development, the pressure on the transportation of urban construction earthwork slurry is increasing. Problems such as environmental pollution and traffic disruption during the transportation process by traditional dump trucks have led to more and more complaints from the public. This requires the development and design of new earthwork transportation methods. Ocean Pump Industry is specialized in the R & D, production, and sales of sand pumps. It has designed and developed a new model of earthwork transportation by pumping sand with sand pumps and pipeline transportation. Through multiple booster pumps, the sand can be transported over tens of kilometers. The following is a detailed explanation of how to select suitable booster type sand transporting pumps.
I. How to Select the Flow Rate and Pipeline Diameter of Booster type Sand transporting Pumps
There are many factors to consider when selecting a suitable booster - type sand - transporting pump. First, calculate the actual flow rate according to the flow rate of the existing sand sucking pump and the transportation distance, or determine how much slurry flow can be provided in the front for the booster type sand transporting pump to suck. After determining the specific flow rate, calculate the pipeline and head requirements according to the transportation distance. The calculation formula is as follows:
1.According to the formula for average flow velocity: V = 4Q/(D²*3600), where Q represents the transportation flow rate and D is the pipeline diameter.
In complex working condition designs, it is necessary to check the pipeline flow velocity and compare to select the best plan. For example, when transporting sand over long distances, focus on checking the flow velocity to control pipeline losses. In addition, when pumps are connected in parallel for drainage, it is necessary to check the pipeline flow velocity when one pump is working and when multiple pumps are working. This is where design problems are most likely to occur when selecting sand pumps for drainage.
II. How to Select the Head of Booster type Sand transporting Pumps
1. Head Calculation Formula
For example, if the customer requires a flow rate of 1818m3/h and a 450 PE pipe is selected for the pipeline, the pipeline loss can be simply calculated as follows:
(Here, the content about the figure for pipeline loss calculation is missing in the original text. If there is relevant information, it should be added in detail).
Through calculation, the pressure and flow velocity values can be obtained. The obtained flow velocity value should be consistent with the value calculated from the flow rate and pipeline diameter in the first step. Select the head of the sand pump according to the pressure requirement, and also consider three parameters: the vertical transportation height difference, pipeline loss, and head safety margin.
The pipeline loss is greatly affected by the inner diameter of the pipeline and the flow velocity of the medium. In addition, it is also affected by the pipeline material (inner wall friction coefficient), slurry concentration, slurry viscosity, pipeline length, pipeline bending conditions, and pipe fittings such as valves. Therefore, for drainage working conditions with sand in water, the pipeline loss is much larger than that of clean water. Moreover, the higher the slurry concentration and viscosity, the greater the pipeline loss. When designing and selecting, the pipeline loss can be first calculated under the condition of clean water, and then multiplied by 1.5 - 3 times as the pipeline loss for selection. HDPE pipes are generally recommended for the drainage pipelines of sand pumps, as they have a relatively small friction coefficient and low pipeline losses.
Regarding the head safety margin, when there is sand in the water, the long - term use of the water pump will cause wear, resulting in a decrease in flow rate and head. When the maximum head of the sand pump is less than the working head, it cannot meet the transportation requirements. Therefore, a wear margin should be reserved for the head when selecting a sand pump. In addition, since the pipeline loss of the sand pump is calculated by doubling the pipeline loss under the clean - water condition, which is an empirical conclusion, a design reserve for the head also needs to be considered for uncertain working condition designs. This is also one of the differences between the design and selection of clean water pumps and sand pumps.
After determining the rated head of the sand pump, it is also necessary to further check the rated flow rate of the sand pump. Since the actual operating head is lower than the rated head, the actual flow rate is larger than the rated flow rate. It is necessary to check the rated flow rate and the actual flow rate according to the performance curve of the product. If the difference is not significant, directly select the rated flow rate according to the design flow rate (as the sand pump wears, the actual flow rate will gradually decrease, so a certain margin should also be reserved); if the difference is too large, the selected rated flow rate of the sand pump should be less than the design flow rate.
III. Determine the Slurry Density and Solid Concentration, and Select an Appropriate Power Source (Motor or Diesel Engine)
The output power of the sand pump P = QH, where is the density of the slurry transported by the pump; g is the acceleration due to gravity; Q is the flow rate of the pump; H is the head of the pump.
When selecting a sand pump, the slurry density must be considered. Different slurry densities require different motor or diesel - engine powers. When selecting, the accurate way to obtain the slurry concentration is to measure it on - site. During the operation of the sand pump, take a sample at the outlet with a container, and calculate the solid weight ratio by weighing, or check the solid volume ratio after sedimentation, and then calculate the solid weight ratio according to the solid specific gravity.
It should be noted that when selecting a sand - pump product, on the premise that it meets the requirements of slurry density and concentration, it is also necessary to consider the actual situation of the slurry and select products with different wear resistance levels. One is to meet the service life requirements, the other is to take into account economic efficiency, and try to reduce the frequency of spare part replacement and downtime for maintenance to ensure the continuity of construction.
IV. Other Factors
When selecting a suitable sand pump, it is also necessary to understand whether there are impurities such as cobblestones or garbage in the transported medium. The main reasons are as follows:
1. Limited by the impeller passage and the number of blades, the passage - through capacity of each pump type is different, and the maximum passage through diameter should be indicated. When selecting, determine the maximum particle diameter first, and then select the pump type or change the number of blades. Make a sand sucking head according to the determined pump type.
2. Ocean sand pumps are specially designed with large particle sand pumps, which are suitable for sand sucking environments with more cobblestones or garbage, improving the passage through capacity and avoiding pipeline blockage.
3. If there are long fiber impurities in the water, measures such as lengthening the filter screen or using a double layer filter screen can be taken to prevent the filter screen from being blocked, resulting in the pump not discharging water. For media with special discharge requirements, a customized plan is required.
All of these considerations are about the solid passing capacity to avoid pipe and pump blockages, so as to maximize the advantages of the sand pump, ensure the normal operation of the equipment, and provide users with a better using experience.
Conclusion
By reasonably arranging booster pumps, the discharge distance can be significantly extended (20km+), which is suitable for long distance sand transportation, tailings discharge, and other projects. The key steps are:
1. Calculate the pipeline friction loss and required head.
2. Select a matching booster pump (with the same flow rate and sufficient head).
3. Optimize the installation location and adopt automated control.
If specific calculations or pump selection suggestions are needed, please provide:
- Pipeline length, diameter, and material
- Slurry concentration and flow rate
- Terrain elevation changes
We can help you design the optimal booster - pump solution!
TAIAN OCEAN PUMP CO.,LTD
DORIS CHEN
oc@tsbeng.com
whatsapp : +86 18562293319
-
WhatsApp
-
E-MailE-Mail:oc@tsbeng.com
-
WeChatWeChat:yychen19