Everything You Need to Know About Gravel Pump
Gravel pumps may not be the most glamorous pieces of equipment, but they play a crucial role in various industries, from mining to construction and dredging. These robust machines are designed to handle the challenging task of moving abrasive materials like gravel, sand, and slurry with efficiency and precision. If you’ve ever wondered how these pumps work or why they are essential, you’ve come to the right place.
In this comprehensive guide, we will delve into the world of gravel pumps, exploring their functions, applications, advantages, and more. Whether you’re a professional in the mining field, a construction enthusiast, or simply curious about this specialized equipment, we’ve got you covered.
From understanding the inner workings of gravel pumps to exploring the factors to consider when choosing the right one, we will equip you with the knowledge needed to make informed decisions and operate gravel pumps effectively. So, let’s embark on a journey through the intricate world of gravel pumps and discover why they are indispensable in various industries.
Tai’an Ocean Pump is a renowned manufacturer in the field of gravel pumps, offering reliable and high-performance equipment for various industries. If you’re seeking comprehensive information about Tai’an Ocean Pump’s gravel pump and its applications, you’ve come to the right place.
Whether you’re involved in mining, dredging, or construction projects, understanding the capabilities of this gravel pump will empower you to make informed decisions and optimize your operations.
Tai’an Ocean Pump’s commitment to quality and innovation has solidified its reputation as a trusted provider of gravel pumps. By delving into the intricacies of their gravel pump, we aim to equip you with the knowledge necessary to leverage this equipment effectively and achieve exceptional results.
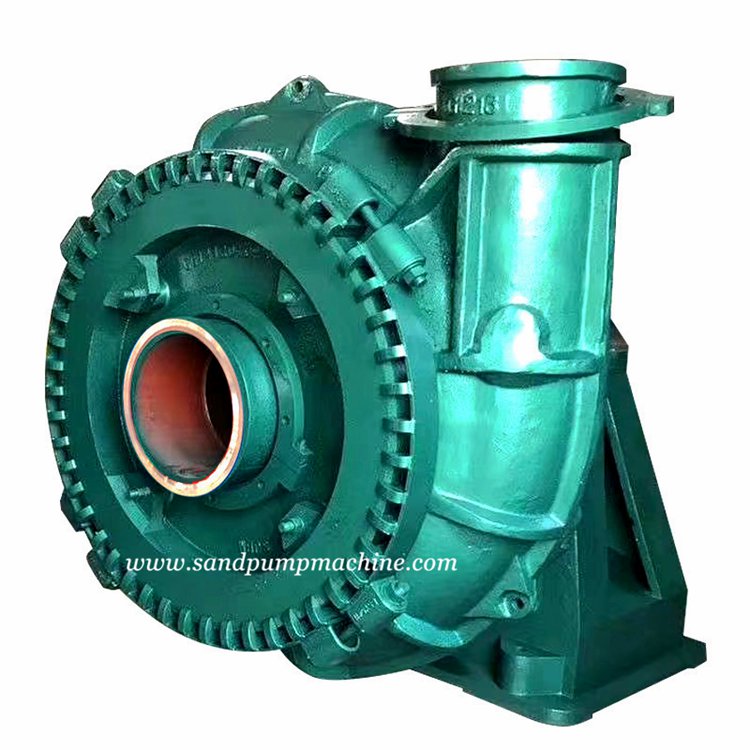
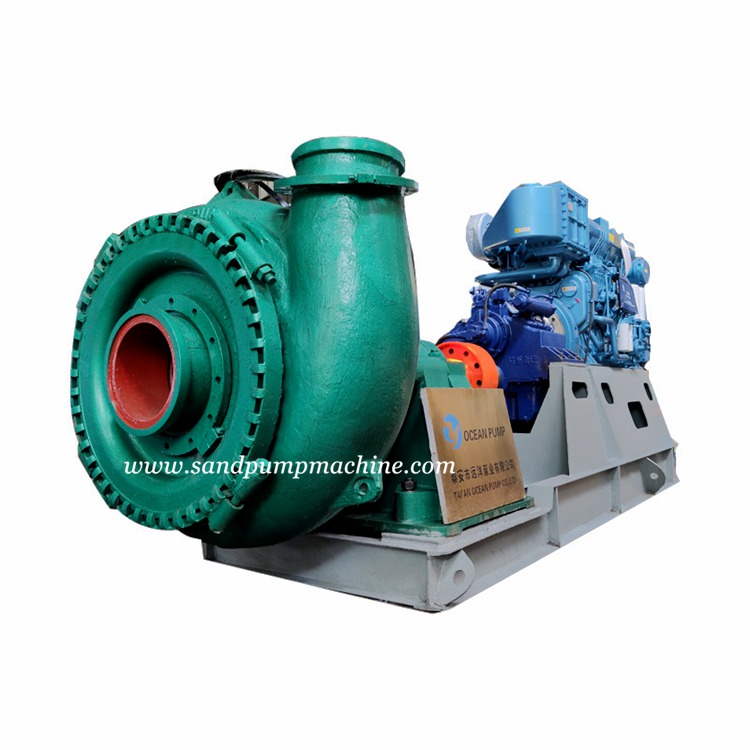
What is a Gravel Pump?
A gravel pump is a specialized type of pump designed to handle and transport abrasive materials, particularly gravel, sand, and slurry. It is widely used in industries such as mining, dredging, and construction, where the efficient movement of these materials is essential.
Gravel pumps are typically centrifugal pumps, which means they use rotating impellers to create centrifugal force and propel the material through the pump. These pumps are specifically designed to withstand the harsh conditions associated with handling abrasive materials, such as high solids content, large particle sizes, and corrosive environments.
Key Components of a Gravel Pump
A gravel pump consists of several key components that work together to facilitate the handling and transportation of abrasive materials. Let’s take a closer look at these components and how they function:
- Impeller: The impeller is a rotating component with vanes or blades that create centrifugal force. As the impeller spins, it imparts kinetic energy to the fluid, pushing it outward and generating pressure.
- Casing: The casing is a stationary housing that surrounds the impeller. It directs the flow of the material and helps maintain the efficiency of the pump. The casing often has a wear-resistant lining to withstand the abrasive nature of the pumped material.
- Suction Pipe: The suction pipe connects to the inlet of the pump and is responsible for drawing in the material from the source. It may include a strainer or screen to prevent large debris from entering the pump.
- Discharge Pipe: The discharge pipe is connected to the outlet of the pump and transports the material to the desired location. It may include additional fittings or valves to control the flow rate and direction.
- Motor or Diesel Engine: The motor or power source provides the necessary energy to drive the pump. Gravel pumps can be powered by electric motors or diesel engines, depending on the specific application and requirements.
How Does a Gravel Pump Work?
The operation of a gravel pump can be summarized in the following steps:
- Priming: Before starting the pump, the suction pipe and casing need to be filled with fluid to create a vacuum. This process is known as priming and ensures that the pump can effectively draw in the material.
- Material Intake: Once the pump is primed, the rotating impeller creates a centrifugal force that draws the material into the pump through the suction pipe. The impeller blades accelerate the material, increasing its velocity.
- Centrifugal Action: As the material enters the casing, the curved shape of the casing and the high-speed rotation of the impeller cause the material to move in a circular motion. The centrifugal force generated by the impeller pushes the material towards the casing walls.
- Pressure Generation: The material is then forced out through the discharge pipe due to the increasing pressure within the casing. This pressure is a result of the centrifugal force and the design of the pump components, including the impeller and casing.
- Material Transport: The material is transported through the discharge pipe to the desired location, where it can be deposited or further processed as required.
Gravel pumps are designed to handle abrasive materials efficiently and reliably, thanks to the combination of centrifugal force and durable components that can withstand the wear and tear caused by the particles being pumped.
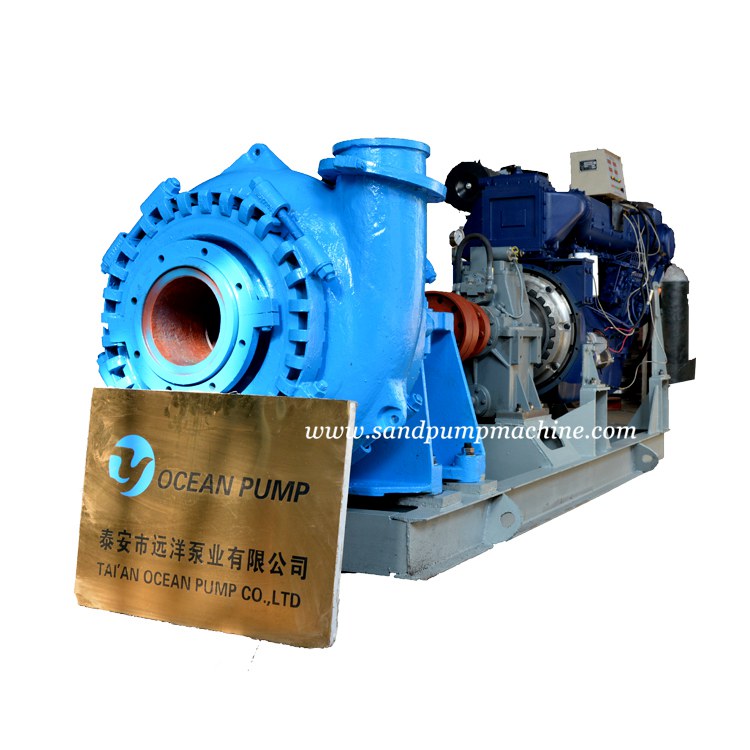
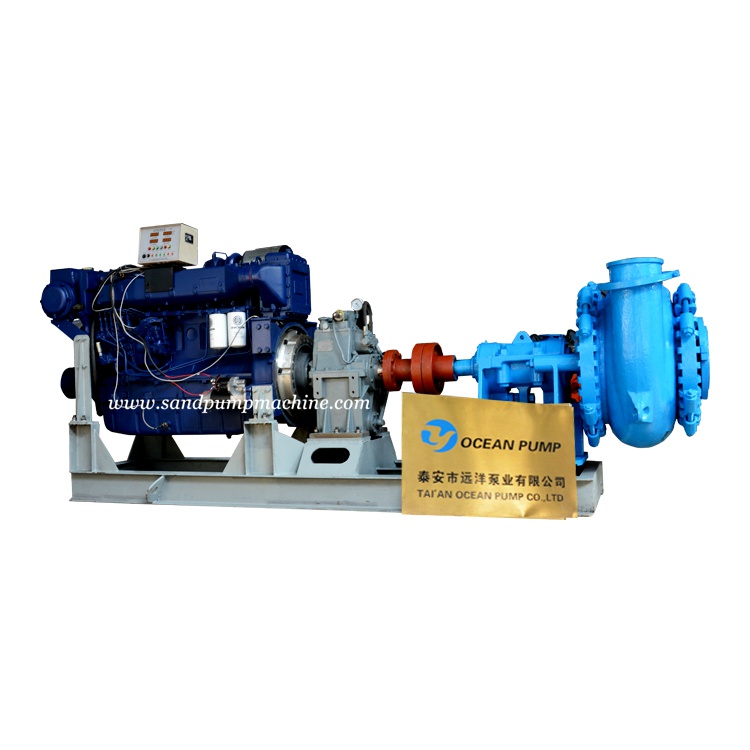
Different Types of Gravel Pumps
There are different types of gravel pumps available, each designed with specific features and capabilities to suit various applications. Here are some common types of gravel pumps:
- Horizontal Centrifugal Gravel Pump:This is the most common type of gravel pump, featuring a horizontal shaft and an impeller that rotates within a horizontal casing. These pumps are widely used in mining, dredging, and construction for handling gravel, sand, and slurry.
- Vertical Centrifugal Gravel Pump: Unlike horizontal pumps, vertical gravel pumps have a vertical shaft and impeller arrangement. They are primarily used in applications where the pump needs to be submerged in the fluid being pumped, such as in underwater dredging or sump pumping.
- Submersible Gravel Pump: Submersible gravel pumps are designed to be fully submerged in water or other fluids. They are often used in dredging operations, underwater mining, and other applications where the pump needs to operate in deep water or in environments with limited access.
- Dredge Pump: Dredge pumps are specifically designed for dredging operations, which involve removing sediment, sand, and other materials from bodies of water. These pumps have a robust construction with large impellers and high power capacity to handle the demanding conditions of dredging projects.
- Slurry Pump: While not exclusively designed for handling gravel, slurry pumps are capable of effectively moving abrasive mixtures of solids and liquids. They are commonly used in mining, mineral processing, and other industries where slurries with high solids content need to be transported.
Applications of Gravel Pumps
Gravel pumps find a wide range of applications in various industries due to their ability to handle abrasive materials efficiently. Here are some common applications of gravel pumps:
- Mining: Gravel pumps are extensively used in mining operations for the extraction and transportation of minerals and ores. They are particularly useful in alluvial mining, where gravel and sand deposits are processed to recover valuable minerals such as gold, tin, and diamonds. Gravel pumps are employed to pump the slurry containing the mined material, allowing for efficient separation and processing.
- Dredging: Gravel pumps play a vital role in dredging projects, which involve removing sediment, silt, sand, and other materials from water bodies like rivers, lakes, and harbors. Dredging pumps are used to extract and transport the dredged material, facilitating channel maintenance, land reclamation, and navigation improvement. Gravel pumps are capable of handling the large volumes of solids and slurry encountered in dredging operations.
- Construction: Gravel pumps are utilized in construction projects that involve the transfer of sand, gravel, and other aggregates. They are commonly used in applications such as foundation building, land reclamation, and the creation of artificial islands. Gravel pumps enable efficient material transportation on construction sites, ensuring a steady supply of aggregates for various construction processes.
- Sand and Gravel Industry: In the sand and gravel industry, gravel pumps are employed to extract and transport sand and gravel deposits from rivers, streams, and quarries. These pumps enable the efficient processing of these materials for use in construction, concrete production, and other industrial applications.
- Industrial Processing: Gravel pumps find application in various industrial processes that involve the handling of abrasive slurries. Industries such as mineral processing, coal washing, chemical processing, and power generation utilize gravel pumps to transport materials like coal, minerals, and chemical slurries through their production systems.
- Environmental Cleanup: Gravel pumps are used in environmental cleanup operations to remove sediment, debris, and pollutants from water bodies. They play a crucial role in restoring and maintaining the ecological balance in rivers, lakes, and other aquatic environments.
The versatility and robustness of gravel pumps make them indispensable in these industries, allowing for efficient handling and transportation of abrasive materials in a wide range of applications.
Advantages of Gravel Pumps
Gravel pumps offer several advantages that make them the preferred choice in various industries for handling abrasive materials. Here are some key advantages of using gravel pumps:
- Efficient Handling of Abrasive Materials: Gravel pumps are specifically designed to handle abrasive materials such as gravel, sand, and slurry. Their robust construction and wear-resistant components, such as hardened impellers and casings, enable them to withstand the erosive effects of abrasive particles. This allows for efficient and reliable material transportation without significant wear and tear on the pump.
- High Solids Handling Capability: Gravel pumps are capable of handling high concentrations of solids in the pumped fluid. They can effectively transport mixtures with a high solids-to-liquid ratio, making them ideal for applications where the content of solids is significant. This ensures that the pump can handle demanding tasks such as mining, dredging, and processing of slurries containing large particles.
- Versatility in Applications: Gravel pumps find versatile applications in various industries. They can be used in mining, dredging, construction, sand and gravel operations, mineral processing, and more. The ability to handle different materials and adapt to different environments makes gravel pumps a valuable asset in numerous industries and applications.
- Flexibility in Pumping Distance and Elevation: Gravel pumps offer flexibility in pumping distance and elevation. They can transport materials over long distances, allowing for efficient material transfer from the source to the desired location. Additionally, some gravel pumps are capable of pumping materials vertically, making them suitable for applications such as underwater dredging or pumping from deep pits.
- Easy Maintenance and Repairs: Gravel pumps are designed for easy maintenance and repairs. Their components can be readily accessed, allowing for quick inspection, maintenance, and replacement if necessary. This reduces downtime and ensures that the pump can be kept in optimal working condition with minimal effort.
- Customizable Configurations: Gravel pumps can be customized to meet specific requirements. They are available in different sizes, power capacities, and configurations to suit different applications and operating conditions. This allows for the selection of a gravel pump that precisely matches the needs of the project, optimizing efficiency and performance.
The advantages of gravel pumps make them indispensable in industries that deal with abrasive materials, enabling efficient material handling, high solids transport, and versatility in a wide range of applications.
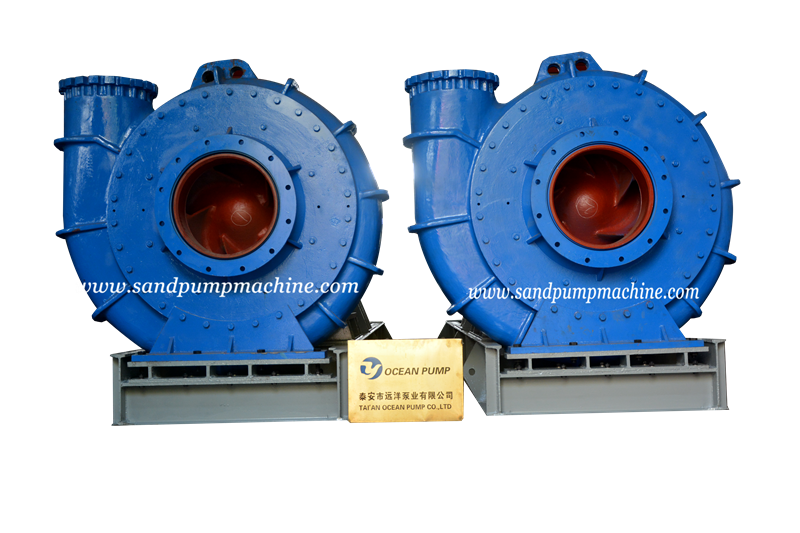
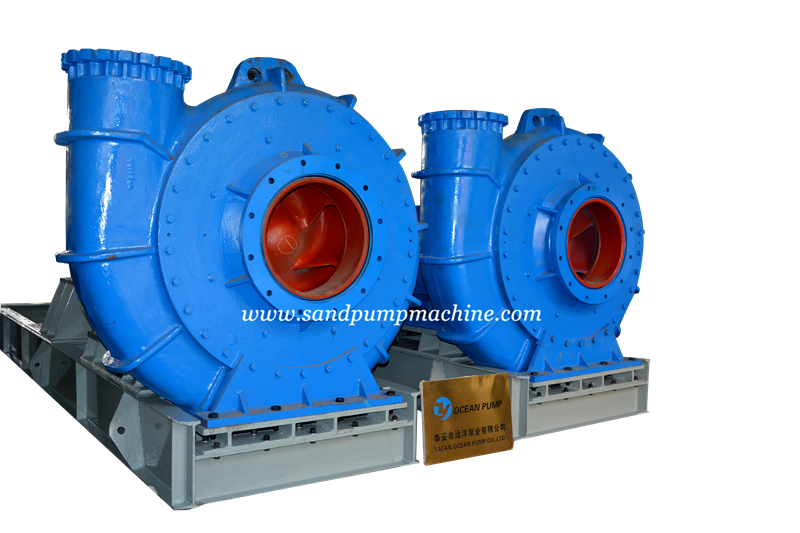
Factors to Consider When Choosing a Gravel Pump
When selecting a gravel pump for a specific application, several factors should be taken into consideration. Here are some key factors to consider when choosing a gravel pump:
- Particle Size and Abrasiveness: Consider the size and abrasive nature of the particles you will be pumping. Different pumps are designed to handle specific particle sizes and abrasive conditions. Ensure that the selected pump is capable of efficiently handling the size and abrasiveness of the materials in your application.
- Flow Rate and Head: Determine the required flow rate (volume of material per unit of time) and head (vertical distance or pressure required to pump the material). It is essential to choose a gravel pump that can meet the desired flow rate and head requirements. Consider the pump’s performance curve to ensure it matches your specific needs.
- Solids Handling Capacity: Evaluate the solids handling capacity of the pump, which refers to the maximum concentration of solids it can effectively handle. This is typically expressed as a percentage of solids by weight. Ensure that the pump can handle the desired solids concentration in your application without clogging or excessive wear.
- Pump Efficiency: Efficiency is an important factor to consider, as it directly impacts the operating costs and overall performance of the pump. Look for a gravel pump with high efficiency to minimize energy consumption and maximize the output.
- Pump Construction and Materials: Consider the construction and materials of the pump. The pump components, such as impellers, casings, and liners, should be made from wear-resistant materials capable of withstanding the abrasive nature of the pumped material. Also, ensure that the pump is robustly constructed for durability in the specific application and operating conditions.
- Pump Drive and Power Source: Determine the most suitable drive system and power source for your application. Gravel pumps can be powered by electric motors, engines, or hydraulic systems. Consider factors such as availability of power sources, operating environment, and ease of maintenance when selecting the appropriate drive system.
- Maintenance and Serviceability: Assess the ease of maintenance and serviceability of the pump. Look for pumps with easily accessible components, simple maintenance procedures, and availability of spare parts. This ensures that the pump can be properly maintained and serviced, minimizing downtime and optimizing its lifespan.
- Application-specific Requirements: Consider any specific requirements of your application. For example, if you require submersible operation, choose a pump designed for underwater use. If your application involves high-pressure conditions, select a pump capable of handling high pressure.
By carefully considering these factors and matching them to the requirements of your specific application, you can choose a gravel pump that will deliver optimal performance, efficiency, and durability. Consulting with pump manufacturers or experts can also provide valuable insights and guidance in making the right selection.
Proper Operation and Maintenance of Gravel Pumps
Proper operation and maintenance of gravel pumps are essential to ensure their optimal performance, longevity, and reliability. Here are some key guidelines for operating and maintaining gravel pumps:
- Read the Manufacturer’s Manual: Familiarize yourself with the manufacturer’s manual and follow their specific guidelines for operation, maintenance, and troubleshooting. The manual provides valuable information on the pump’s specifications, recommended operating parameters, and maintenance procedures.
- Proper Installation: Ensure that the gravel pump is correctly installed according to the manufacturer’s instructions. This includes proper alignment, secure mounting, and proper connection of all piping and hoses. Improper installation can lead to excessive vibration, premature wear, and reduced performance.
- Monitor Operating Parameters: Regularly monitor and maintain the operating parameters of the pump, such as flow rate, pressure, and temperature. Operating the pump within the recommended parameters helps prevent excessive wear and damage to the components.
- Adequate Lubrication: Follow the manufacturer’s recommendations for lubrication. Ensure that all lubrication points are properly greased or oiled at the recommended intervals. Insufficient lubrication can lead to increased friction, overheating, and premature failure of bearings and other moving parts.
- Regular Inspection: Conduct regular visual inspections of the pump to check for any signs of damage, leaks, or abnormal wear. Inspect the impeller, casing, seals, and other components for wear, erosion, or corrosion. Replace any damaged or worn parts promptly to prevent further damage.
- Clean and Flush: Regularly clean the pump and flush it to remove any accumulated debris, sediment, or abrasive particles. This helps prevent clogging, maintains optimal performance, and reduces the risk of damage to the pump.
- Preventive Maintenance: Implement a preventive maintenance schedule based on the manufacturer’s recommendations. This may include tasks such as regular inspection and replacement of wearing parts, checking and tightening bolts and fasteners, and verifying alignment and balance.
- Handle Pump Cavitation: Cavitation can occur when the pump’s suction pressure drops too low, causing the formation of vapor bubbles that collapse violently, leading to erosion and damage. Take measures to prevent or minimize cavitation, such as ensuring proper suction conditions, maintaining appropriate NPSH (Net Positive Suction Head), and avoiding excessive pump speed.
- Training and Operator Awareness: Provide proper training to the pump operators to ensure they understand the correct operating procedures, safety precautions, and maintenance requirements. Operators should be aware of the limitations of the pump and promptly report any abnormal conditions or performance issues.
- Keep Records: Maintain detailed records of the pump’s operation, maintenance activities, and any repairs or replacements. This helps track the pump’s performance, identify recurring issues, and plan future maintenance and replacement schedules.
By following these guidelines and regularly maintaining the gravel pump, you can maximize its efficiency, minimize downtime, and extend its lifespan, ensuring reliable and cost-effective operation in your application.
Conclusion
Gravel pumps are indispensable tools in various industries for efficiently handling abrasive materials. Their ability to handle high concentrations of solids, versatility in applications, and robust construction make them a reliable choice for tasks such as mining, dredging, construction, and industrial processing. By considering factors such as particle size, flow rate, and pump efficiency, one can select the most suitable gravel pump for their specific application.
Proper operation and maintenance of gravel pumps are crucial for ensuring optimal performance and longevity. Following the manufacturer’s guidelines, conducting regular inspections, and implementing preventive maintenance schedules are key to minimizing downtime and maximizing the pump’s lifespan. Adequate lubrication, proper installation, and monitoring of operating parameters also contribute to the pump’s efficiency and reliability.
With their ability to handle abrasive materials with ease and efficiency, gravel pumps continue to play an integral role in industries worldwide. By understanding their applications, advantages, and proper maintenance procedures, professionals can harness the power of gravel pumps to enhance productivity and achieve successful outcomes in their respective fields.
-
WhatsApp
-
E-MailE-Mail:oc@tsbeng.com
-
WeChatWeChat:yychen19