How to Troubleshoot Some Common Submersible Slurry Pump Problems
Submersible slurry pumps are indispensable tools extensively used across multiple industries due to their ability to handle abrasive, corrosive, and high-density materials. In 2021, the global market for submersible pumps surpassed USD 11.3 billion, and it is projected to exhibit a compound annual growth rate (CAGR) of 6.83% from 2023 to 2028, potentially exceeding USD 16.8 billion by 2027
The market size of the global submersible slurry pumps industry was valued at USD 185.46 million in 2021 and is expected to expand at a CAGR of 6.25% during the period from 2021 to 2027, reaching USD 266.88 million. These pumps are in high demand due to their exceptional durability, which can be attributed to notable features such as a sizable impeller diameter, robust shafts, bearings, and internal passages. Additionally, their lightweight design and ease of maintenance contribute to their popularity in the industry.
Submersible slurry pumps find extensive application across various sectors. They are particularly crucial in the mining industry for handling mining slurries and in dredging operations for removing sediments from water bodies. Construction projects involving tunneling and excavation heavily rely on these pumps. Moreover, in numerous industrial processes that involve abrasive slurries, submersible slurry pumps play a vital role.
This article mainly explains the main parts of Submersible Slurry Pump, its application and how to troubleshoot some common submersible slurry pump problems.
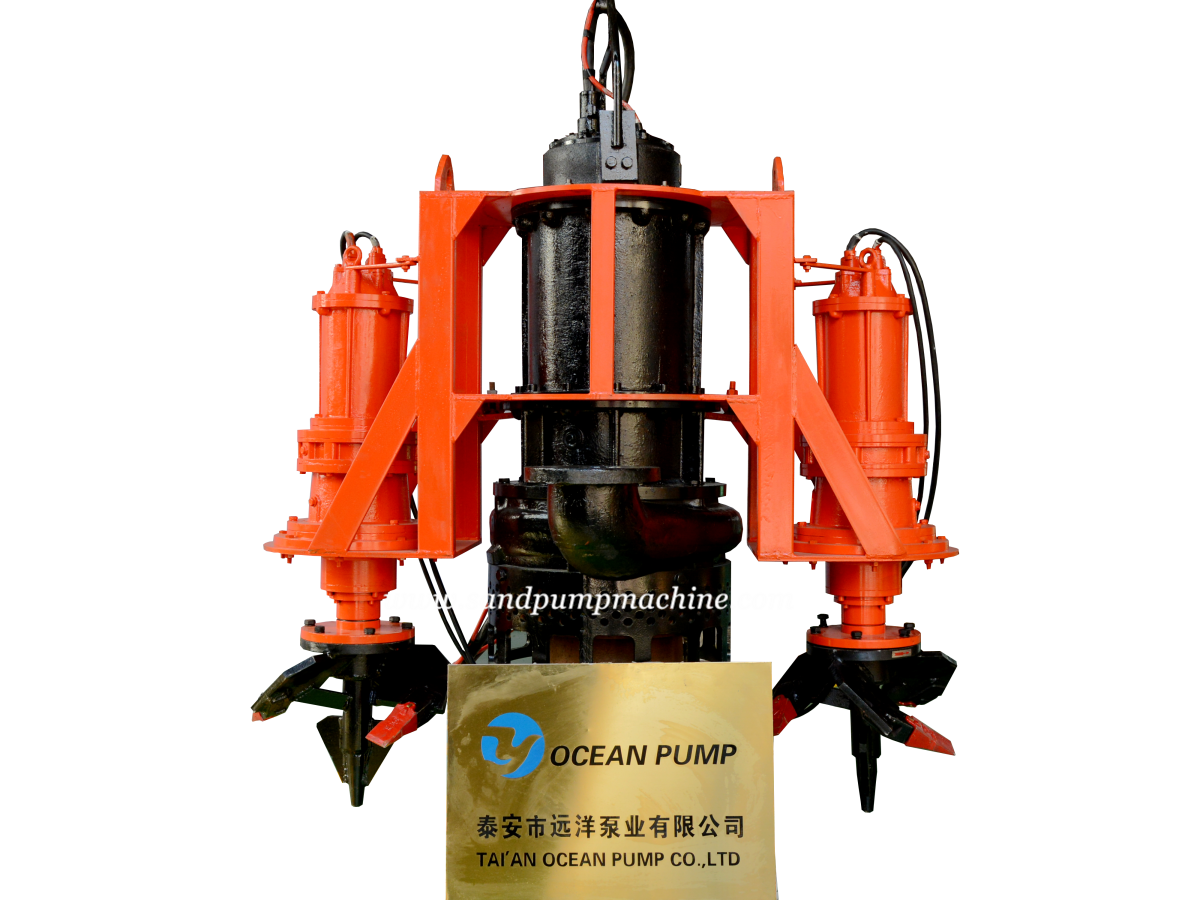
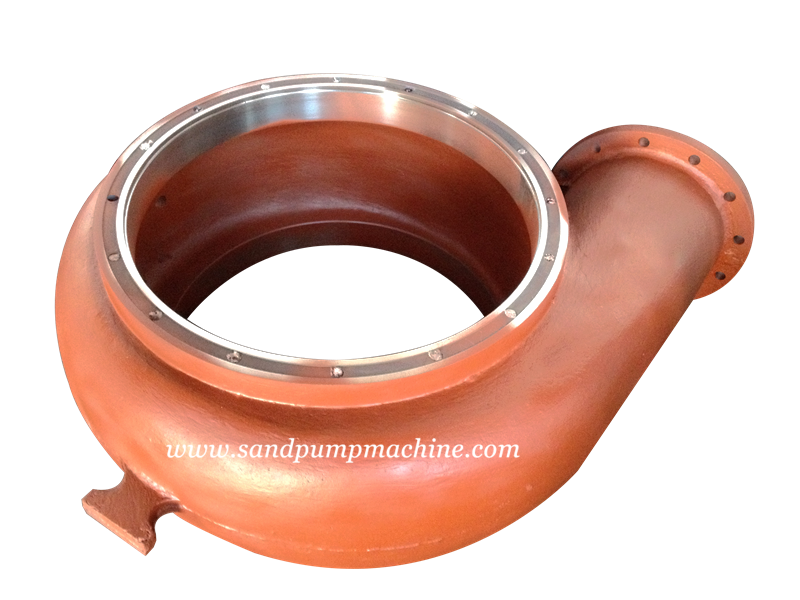
Main Components of Submersible Slurry Pumps
1. Pump Body
It houses the impeller and volute and is designed to withstand the abrasive nature of the slurry.
2. Impeller
The impeller is the rotating component of the pump. It is responsible for moving the slurry through the pump.
3. Volute
The volute is a stationary component that collects the slurry from the impeller and directs it to the discharge outlet.
4. Shaft and Bearings
The shaft connects the impeller to the motor and transmits the rotational motion. Bearings support the shaft and allow it to rotate smoothly.
5. Motor
The motor is typically electric and is sealed to prevent water ingress. It provides the power to drive the impeller and pump the slurry.
6. Seal
The seal prevents the leakage of slurry into the motor compartment. It is a critical component for ensuring the longevity of the pump.
7. Discharge Pipe
The discharge pipe is the outlet for the pumped slurry. It is usually connected to a pipeline or hose for transporting the material to its destination.
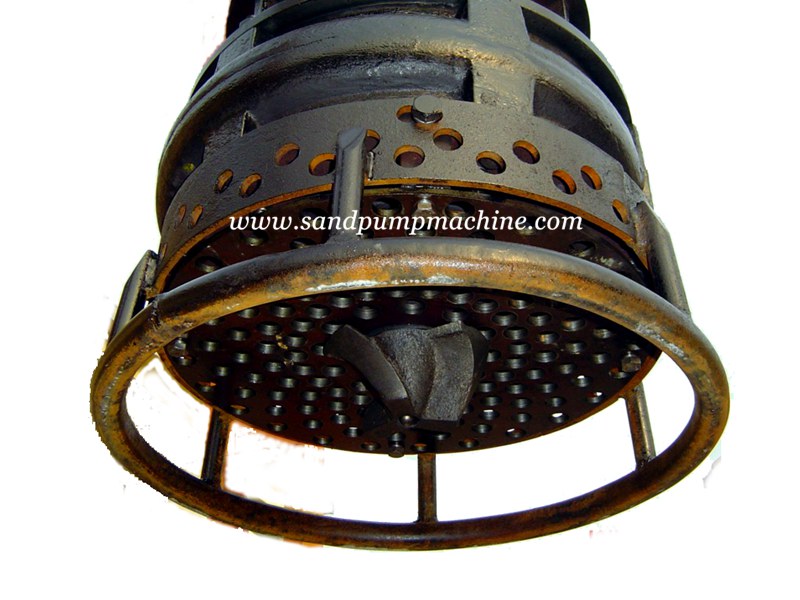
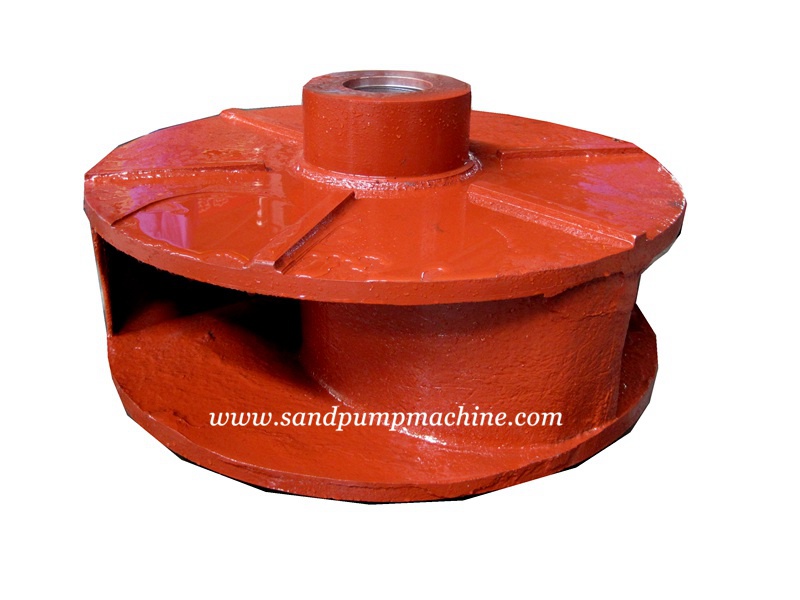
Applications of Submersible Slurry Pumps
1. Mining
The mining industry extensively relies on submersible slurry pumps for multiple purposes. These pumps are primarily employed in dewatering operations, effectively removing water from mining sites. Additionally, they excel at transferring abrasive materials, including tailings and slurries, which are byproducts of mining activities.
2. Construction
Within the realm of construction projects, submersible slurry pumps play a crucial role in managing waterlogged areas. These pumps are adept at pumping out water that is mixed with sand, gravel, and other debris. By efficiently removing excess water from construction sites, they aid in maintaining a safe and productive work environment.
3. Wastewater Treatment
Submersible slurry pumps are integral to wastewater treatment plants, where they are utilized to transfer sludge and other solid materials. The pumps effectively handle the challenging task of transporting these substances, facilitating the treatment process and ensuring efficient wastewater management.
4. Sand and Gravel
In sand and gravel pits, submersible slurry pumps are indispensable. They serve the purpose of transporting materials and removing water from excavation sites. These pumps facilitate the extraction and processing of sand and gravel, ensuring smooth operations and efficient resource utilization.
5. Dredging
Dredging operations extensively rely on submersible slurry pumps to clear silt, sediment, and other unwanted materials from water bodies. These pumps are specifically designed to handle the demanding task of dredging, enabling the removal of accumulated debris and ensuring the navigability and environmental sustainability of waterways.
Submersible slurry pumps find wide-ranging applications across various industries. From the mining sector to construction projects, wastewater treatment plants, sand and gravel pits, and dredging operations, these pumps are essential for efficient material handling, dewatering, and maintaining optimal working conditions. Their robust design and ability to handle abrasive materials make them indispensable tools in these applications, contributing to enhanced productivity and operational effectiveness.
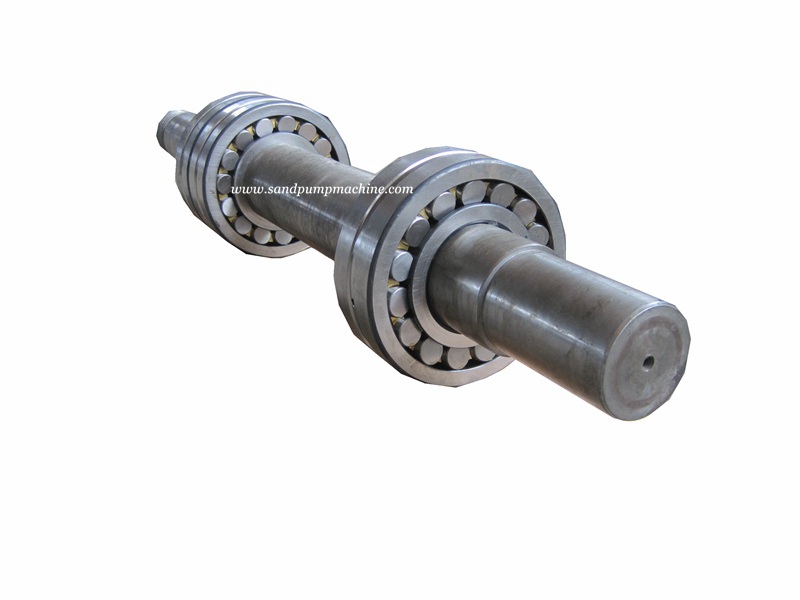
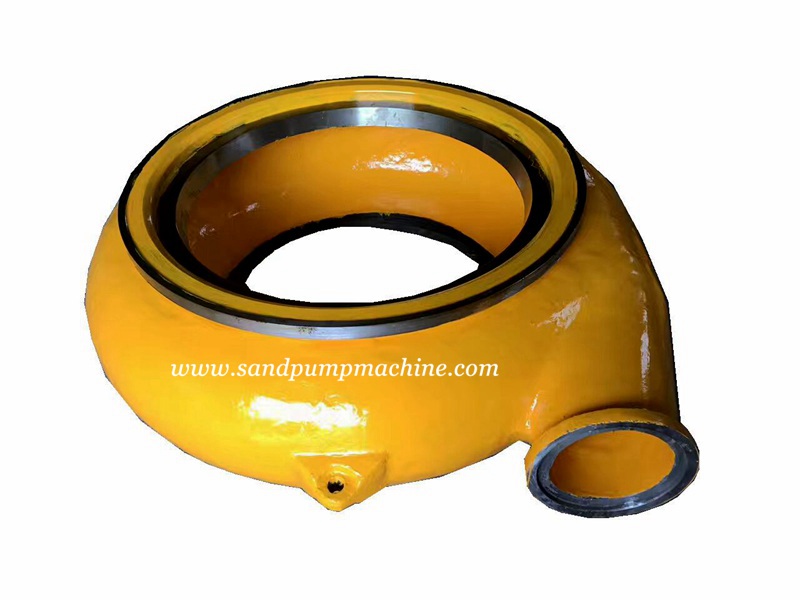
Common Problems of Submersible Slurry Pump and Solutions
1. Temperature Fluctuations
Fluctuations in temperature can indicate underlying issues in a submersible slurry pump. Overheating may be caused by a faulty motor, but it can also result from other factors that affect the pump’s temperature. These factors include:
- Incorrect installation
- Accumulation of foreign materials around the motor
- High or low voltages
- Increase in the ambient water temperature
Failure to address these issues promptly can lead to pump malfunction. Overheating can cause the water or cooling fluid to boil, generating steam that puts pressure on the insulation and leads to ruptures or breakdowns. To prevent overheating, it is important to use durable materials that offer long-lasting and reliable performance. Additionally, ensuring proper fitting of each component is equally crucial.
2. Motor Failure to Start
There are several reasons why a submersible slurry pump’s motor may fail to start. These include:
- Tripped circuit breaker or blown fuse: This can be resolved by replacing the fuse or resetting the circuit breaker.
- Corroded or dirty fuse receptacles: In this case, the motor may stop functioning intermittently. The issue can be resolved by installing new fuse receptacles.
- Debris or corrosion at pressure switch contact points: This can cause voltage fluctuations and motor malfunction. Clearing the debris or corrosion resolves the issue.
- Accumulation of sand or other elements around the pump: This can impede proper functioning, resulting in significantly increased amp readings. Clearing the build-up restores normal motor operation.
3. Voltage Imbalance
Incorrect sizing of drop cables or unequal transmission of voltage to each winding can cause voltage imbalance. This leads to motor overheating and reduces its lifespan, eventually leading to critical failure. To avoid this issue:
- Use properly sized cables.
- Use a motor designed to operate with higher resistance, which requires smaller drop cables and less full load current.
4. Reduction in Supply Line Diameter
Submersible slurry pumps are designed to operate with specific input line diameters. However, using a smaller diameter hose or line with reduction couplings can lead to crimping of the intake line. To avoid this problem:
- Use an intake line of the specified size and ensure the intake and discharge lines have equal sizes.
- Ensure there are no kinks along the length of the intake line from the water source to the pump.
- Use a rigid intake line or non-collapsible hose.
5. Motor Runs Too Often or Constantly
If a submersible slurry pump’s motor cycles frequently or runs constantly, it may be due to:
- System leaks: Damaged pipes need to be replaced, and the water level should be checked to ensure it falls within the pump’s well capacity.
- Defective pressure switch: Examine the settings and clean the contacts to resolve the issue.
- Blocked pump screen or check valve: Removing the blockage solves the problem.
6. Voltage Spike
A sudden voltage spike caused by a lightning strike or storm can damage the motor insulation of a submersible slurry pump, leading to overheating and even holes in the motor casing. Using external surge protection can prevent this problem.
7. Improper Motor Connection
If the impeller of a water pump moves in the wrong direction, the pump cannot operate effectively. This issue may arise from incorrect electrical connections to the electric motor. To rectify the problem, check the motor setup and refer to the user instructions to ensure proper connections.
8. Excessive Noise
Excessive noise from a submersible slurry pump may be a result of cavitation, which occurs when water transfer forms bubbles. Cavitation can reduce pump efficiency and cause excessive noise. To address this, check the valves and ensure the flow pattern hasn’t changed. Additionally, check the alignment between the pump and the driver. Adjustments may be needed to compensate for water viscosity and other characteristics.
Conclusion
A submersible slurry pump comprises various components and is accompanied by numerous additional parts during installation. Consequently, it is susceptible to malfunctioning at any given time. It is imperative to conduct regular equipment inspections, perform maintenance tasks, and promptly replace any damaged parts. By following these recommendations, you can effectively address common issues that may arise with a submersible pump. If you found this article helpful, you can explore more informative articles by visiting Tai’an Ocean Pump.
-
WhatsApp
-
E-MailE-Mail:oc@tsbeng.com
-
WeChatWeChat:yychen19